Weed Electrocution
Weed electrocution, also known as electrical weed control, is a non-selective, non-chemical method in which electricity passes through the plant, including some root tissue, leading to cell rupture and death. Weed electrocution can be highly effective against a broad spectrum of weeds, even at later growth stages, with minimal soil disturbance. Many factors can influence the effectiveness of electrical weed control, including weed density, species, and plant and soil moisture. Electrical weed control is seldom used as a standalone tactic, rather, it is considered a supplemental strategy to other weed management tactics. Use the accordions below to explore more details on this practice.
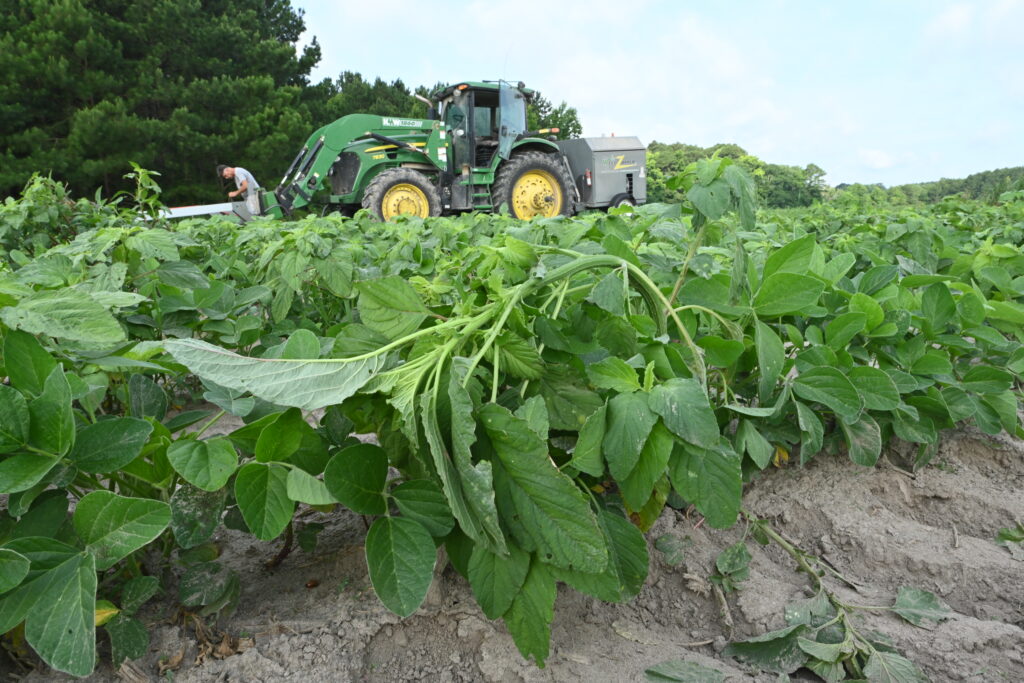
1. What is the history of weed electrocution?
The first versions of electrical weed control emerged in the late 1800s, with the first U.S. patent registered in 1890. However, research in row crops using electrical weed control didn’t begin until the 1970s, with a study by Dr. Michael Diprose in sugar beets. Diprose worked with the first commercially available electrical weeder, manufactured in the 1980s, and marketed as the Lasco LW5 Lightning Weeder. Fast-forward to today, and several iterations of weed electrocution units are commercially available from multiple manufacturers.
2. How does weed electrocution kill weeds?
Weed electrocution units transfer high-voltage electrical current into targeted plants. The high-voltage current passes through plant and root tissues and then into the ground. The plant material acts as a resistor, converting the electrical current into heat. The heat results in membrane disruption, cell rupture, and eventual plant death.
Currently, two types of electrical weed control tools are commercially available: spark-discharge and continuous electrode-contact. Both types can deliver similar amounts of electric current but differ in how it is transmitted. The spark-discharge unit, which was the initial design for this technology, discharges a high-voltage current when weeds come into contact with a single electrode. The electrode is often a copper bar placed above the crop so that current only reaches weeds taller than the canopy (Figure 2).
The continuous-contact units create a circuit between two sets of electrodes, the weed and the soil (Figure 3). The electrodes drag along the ground, delivering current to any plants that come into contact (Figure 4). Continuous-contact electrical weeders can be used for burndown prior to planting or, if shielded, can only target weeds between crop rows. Both types of electrical weeders are powered by the tractor power take-off (PTO) and are effective in various cropping systems.
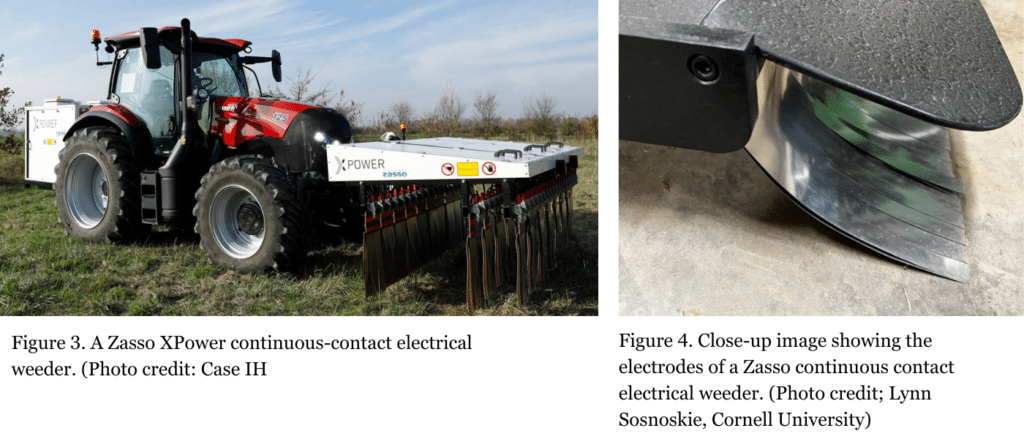
3. What weed species and row crops are best suited to weed electrocution?
The suitability of weed electrocution is highly dependent on the type of machine (spark-discharge or continuous electrode-contact) and the cropping system.
Spark-discharge electrical weed control:
The spark-discharge method is used in row crops such as soybeans and even some vegetables, when the weeds are taller than the crop canopy. The spark discharge method uses an unshielded electrode ranging from 20 to 40 feet long that is positioned above the crop canopy (Figure 2).
Research results from the University of Missouri demonstrated that a spark-discharge electrical weeder called the Weed Zapper (Old School Manufacturing) provided the best control of waterhemp in soybeans (achieving 96% control 42 days after treatment). This level of control was most effective when there were consistent height differences between the crop and the weed, which occurred at the R6 soybean stage in this study. Conversely, waterhemp control was much lower (54% control at 42 days after treatment) when the plants were shorter than the crop.
The researchers also tested the machine on various summer annual broadleaf weeds and found that it provided over 95% control of horseweed, common ragweed, and giant ragweed. This level of control was achieved when the weeds were pollinating or at seed set and were well above the soybean canopy. Similar control (greater than 95%) was achieved on grass species such as barnyardgrass, giant foxtail, and yellow foxtail at reproductive growth stages (flowering, pollination, and seed set). This study also found that efficacy across all species was greatest when plant moisture was higher, and the plants were not under drought stress. The researchers also reported that targeting weeds at later growth stages, either during or after seed development, reduced seed viability by 54 to 80%, depending on the species. As demonstrated by research at Cornell University, the downside to this timing is that weeds will have already competed with the crop prior to control, potentially resulting in yield losses. Additionally, the spark-discharge method of electrical weed control would not be compatible with shorter weed species that persist below the crop canopy.
Continuous-contact electrical weed control:
The continuous-contact electrical weed control units are often designed to be deployed on smaller weeds in fallow, roadside or other non-crop environments, or orchards and vineyards (Figures 2, 4, and 5). Inter-row units are currently being developed and tested in vegetable and agronomic crops. To date, there is little published research using continuous-contact electrical weeders. Preliminary findings have reported that continuous-contact electrocution is equally effective on both grasses and broadleaf weeds when weeds are under 10 inches tall. For larger weeds, slow travel speeds or multiple passes will likely be needed for effective control.
Research at Oregon State University has focused on perennial weed control in blueberry and hazelnut. The results showed that a single treatment applied at a slower operational speed (less than 1 mph), provided effective initial control of Canada thistle, although some regrowth was observed over time. Two or three consecutive passes at a faster speed (1 to 2 mph) over a four-week interval significantly improved effectiveness, achieving up to 90% control. The continuous-contact electrical weeder also demonstrated promising results for yellow nutsedge, reducing tuber viability by 43 to 55% depending on application speed and timing, contributing to population declines in subsequent seasons. Multiple passes targeting actively growing shoots were the most effective. Many factors influence this technology’s effectiveness, including weed species, size, density, travel speed, and soil/plant moisture. More research is needed to understand how these parameters influence weed control efficacy with continuous-contact electrical weeders.
4. Where in the row crop growing season does weed electrocution fit best?
The best time to deploy electrical weed control in your weed management system will depend on the crop and the type of electrical weeder. As previously mentioned, spark-discharge weeders require a height difference between the weed and the crop to be effective. In taller crops like corn, where weeds are typically beneath the canopy, the spark-discharge electrocution method would not be feasible for most of the growing season. This method is more suitable for shorter crops such as soybeans, peanuts, and cotton. In soybean, the spark-discharge method seems to fit best later in the season, as a rescue treatment managing tall weeds that have escaped previous weed control methods. Some organic peanut growers are trying to adapt repeated electric weeding starting shortly after planting and continuing until harvest for more complete weed control. To learn more about how one Maryland farmer is using an electrical weeder on his row crops, see the video below:
5. Where is electrical weed control in use now?
Currently, most electrical weeder manufacturers (~6 companies worldwide) are located in Europe and South America and focus on specialty crops such as orchards, vineyards, and berries. However, with increasing interest in non-chemical weed control in row crops, companies are beginning to enter that market.
Current models designed for row crops available in the U.S. include:
Lasco Lightning Weeder – The Lasco weeders use a spark-discharge method and are suitable for short-stature row crops such as soybeans, peanuts, cotton, etc. Application width can vary, but the maximum is 40ft and requires a tractor that has at least 140 PTO horsepower (HP). The applicator and generator hook to a 3-point attachment and are both located behind the tractor (Figure 5). The Lasco weeder has a copper bar electrode that spans the entire operating width of the unit, passing current through any plants that come into contact with it.
The Weed Zapper – The Weed Zapper comes in various sizes and configurations with horsepower requirements ranging from 65 to 275 HP (Figure 6). It uses the spark discharge method and is best suited before crop emergence or on weeds taller than the crop during the season. Short-stature crops like soybeans, peanuts, and cotton will have the longest utility window. The tractor-attached units have a 20- to 30-foot copper bar electrode mounted to the front of the tractor, passing current through any plants that come into contact with it.
crop.zone volt system – The crop.zone system is a continuous-contact electrical weeder that combines three main components: the volt.cube, volt.apply and volt.fuel. The volt.cube is the generator portion that attaches to the back of a tractor and generates electricity using the PTO (Figure 7). The volt.apply is the “boom” portion of the system located behind the volt.cube, which delivers the current to the plants and can range between 30 and 40 feet in width. Lastly, the volt.fuel is a proprietary conductive liquid reported to improve the system’s effectiveness. The volt.fuel is applied via a spray boom attached to the front of the tractor. The volt system is for broadcast only and can be used for preplant burndown of weeds, crop desiccation, and cover crop termination. Although not currently available in the U.S., crop.zone systems are being sold in Europe and Canada, with plans for expansion into the U.S.
The Zasso XPower Series – The Zasso XPower series are continuous-contact electrical weeders for use in various specialty crops such as citrus, orchards, and coffee. The XPS system features either fixed or moveable electrodes that target weeds in the interrow area of crops (Figure 8). Horsepower requirements vary by model but range between 64 to 150. The spring-loaded design allows passive rotation around the stem or trunk of vines and trees. Zasso also has a line of electrical weeders for residential, commercial, and other non-crop areas.
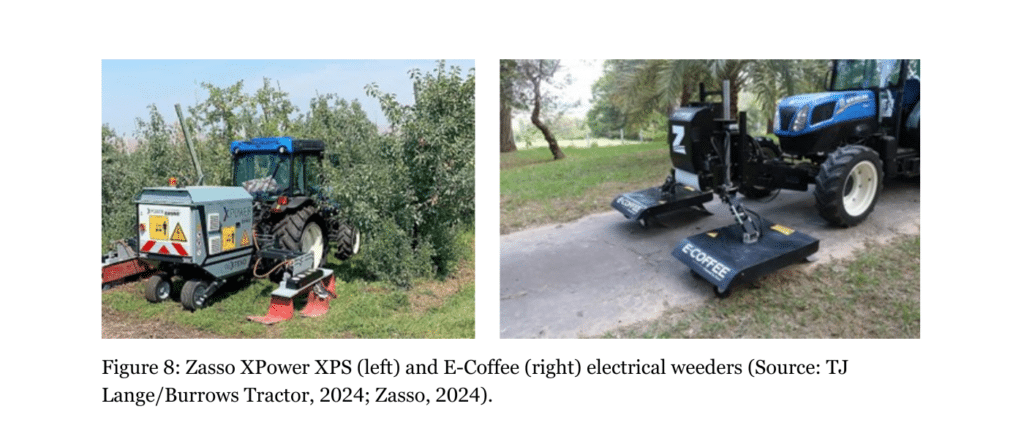
RootWave – The RootWave system is a continuous-contact electrical weeder for use in orchards and vineyards. The RootWave design has electrodes on spring-loaded arms, allowing weed control around the base of trunks (Figure 9). These units require between 64 to 107 HP.
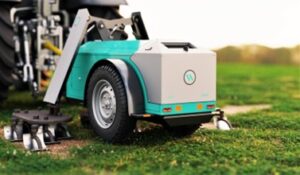
6. What are the risks of weed electrocution?
Weed electrocution methods offer several benefits, but they also present specific risks that must be managed to ensure safe and effective use.
One primary concern is the risk of electrical hazards. Electrical weed control equipment operates at high voltage, and improper handling can lead to severe electrical shocks to operators or nearby individuals. To mitigate this risk, all operators must receive thorough training in equipment operation, including safe handling and operational protocols. Protective gear, such as insulated gloves and boots, is essential during use, and individuals should maintain a safe distance from operating equipment. Regular equipment maintenance and inspections are crucial to identify potential faults, and electrical weed control should not be used in wet or rainy conditions, as moisture increases the likelihood of accidental discharge.
Another significant risk is the potential for fire. Sparks generated by electrical weed control equipment can ignite dry vegetation, particularly in low rainfall areas, under drought conditions, or during periods of low humidity. Critical safety measures include maintaining a safe working perimeter and having fire suppression tools, such as fire extinguishers or water sources, readily available.
Additionally, improper application of electrical weed control can result in unintended crop damage. The high-intensity electric currents used to control weeds may harm crops if not positioned correctly, which could harm yield and quality. To minimize such outcomes, operators must adhere to recommended application speeds and ensure precise targeting of weeds.
Finally, an area of potential concern for farmers and researchers has been the risk of off-target injury to beneficial soil organisms and insects. However, preliminary research from both the University of Missouri and Cornell University has reported no impact on the health of beneficial soil organisms such as earthworms and microbes after the application of both a spark-discharge electrical weed control unit and a continuous-contact electrical weeder.
By addressing these risks with proactive measures, growers can safely integrate weed electrocution into their management practices, maximizing its benefits while safeguarding against potential hazards.
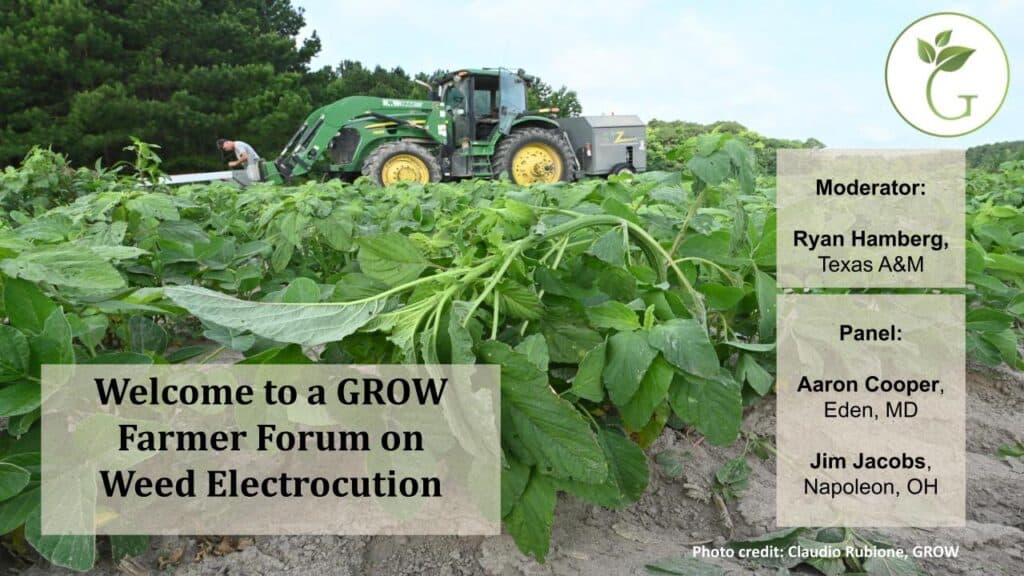
Farmer Forum Recap: Weed Electrocution in the Field
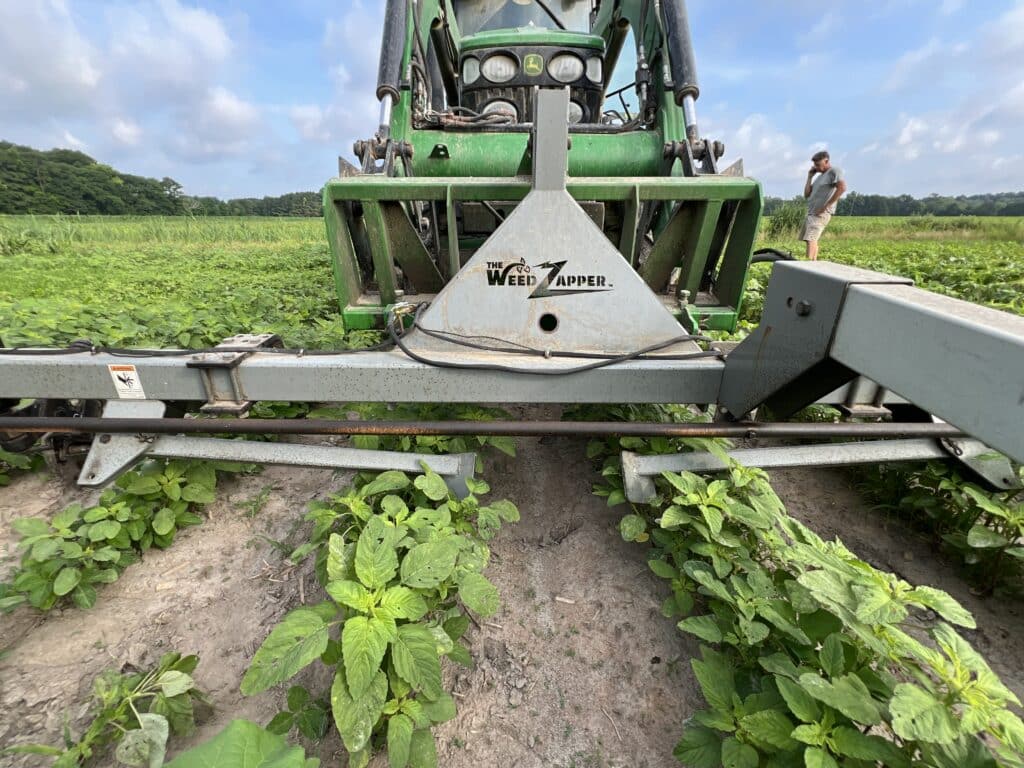
Join a GROW Farmer Forum on Weed Electrocution in the Field
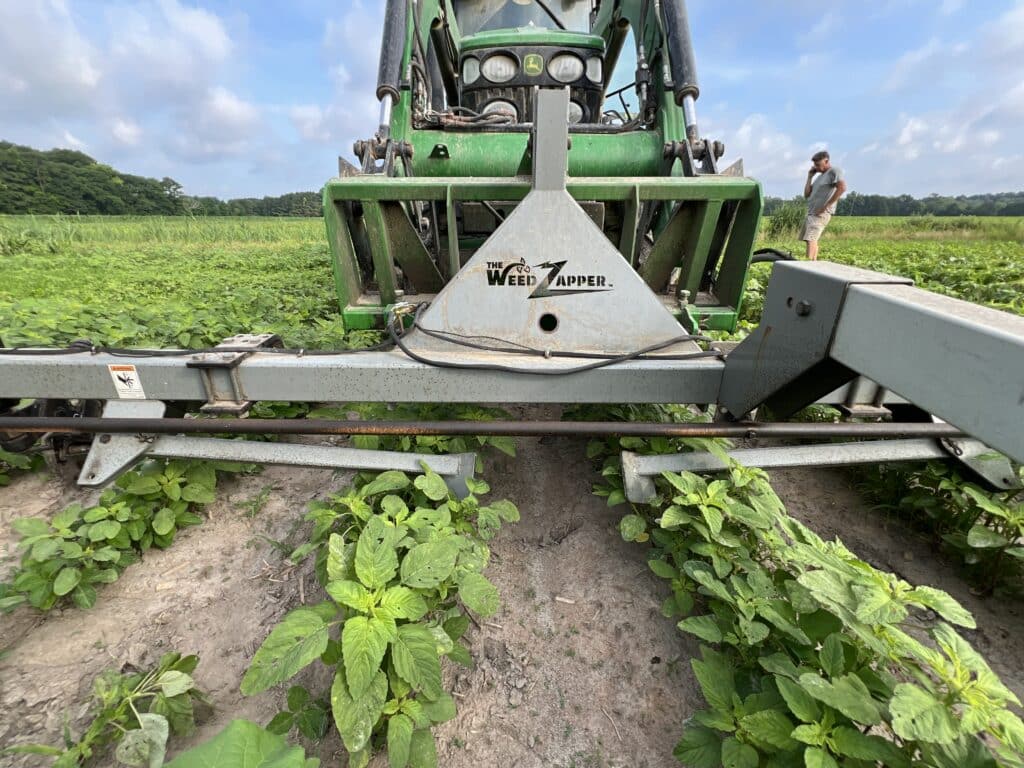
Join a GROW Farmer Forum on Weed Electrocution in the Field
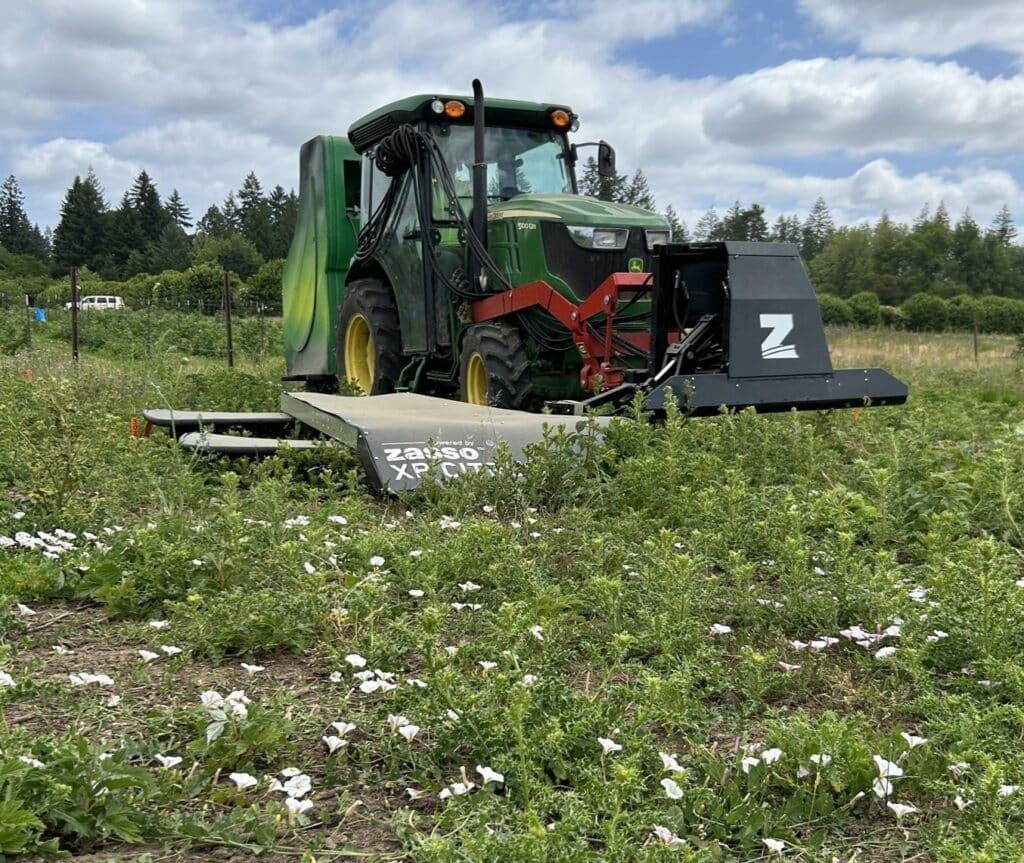
Slow the Cycle: Targeting Perennial Weeds with Weed Electrocution
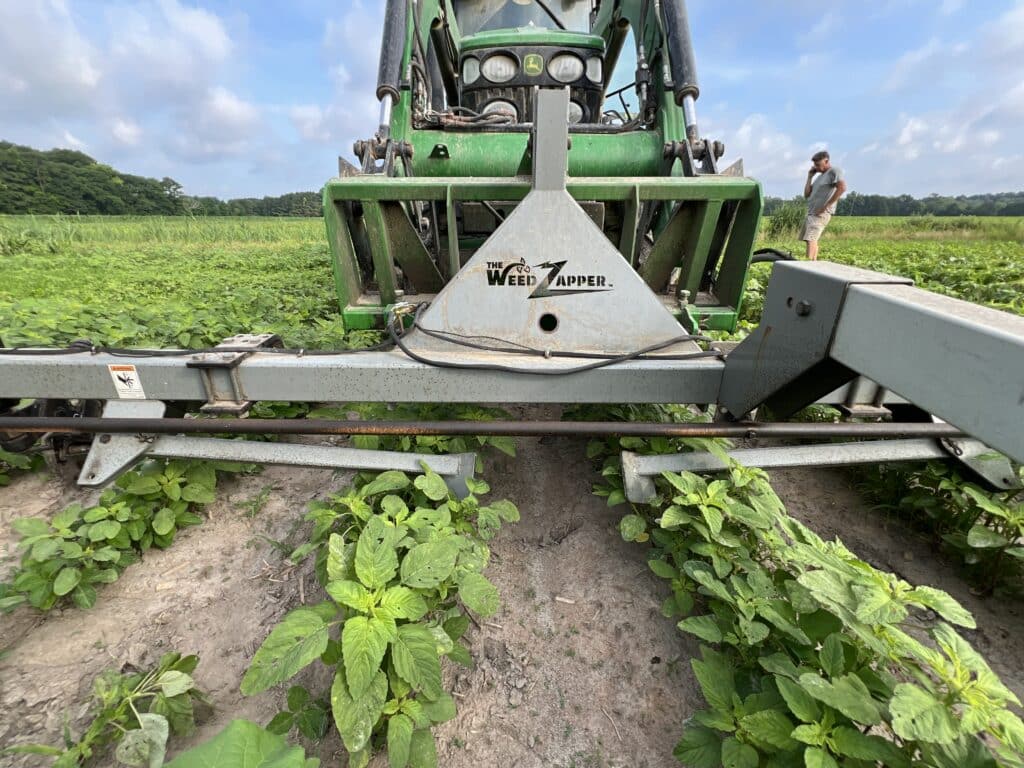
Zap on Over to GROW’s New Weed Electrocution Page
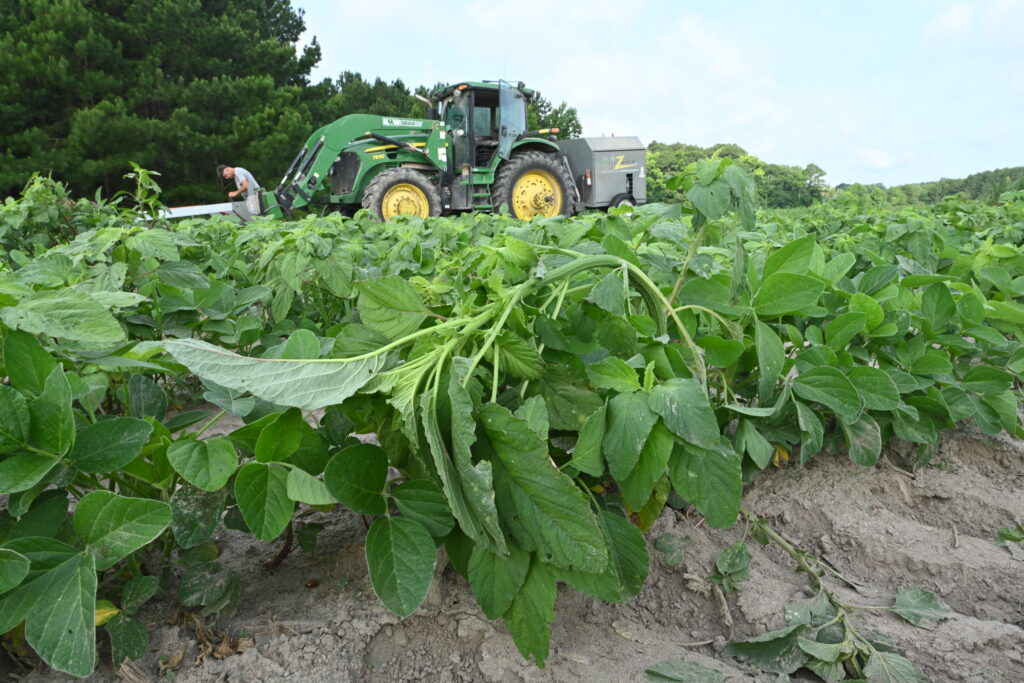
How Weed Electrocution Fits into a Maryland Farm
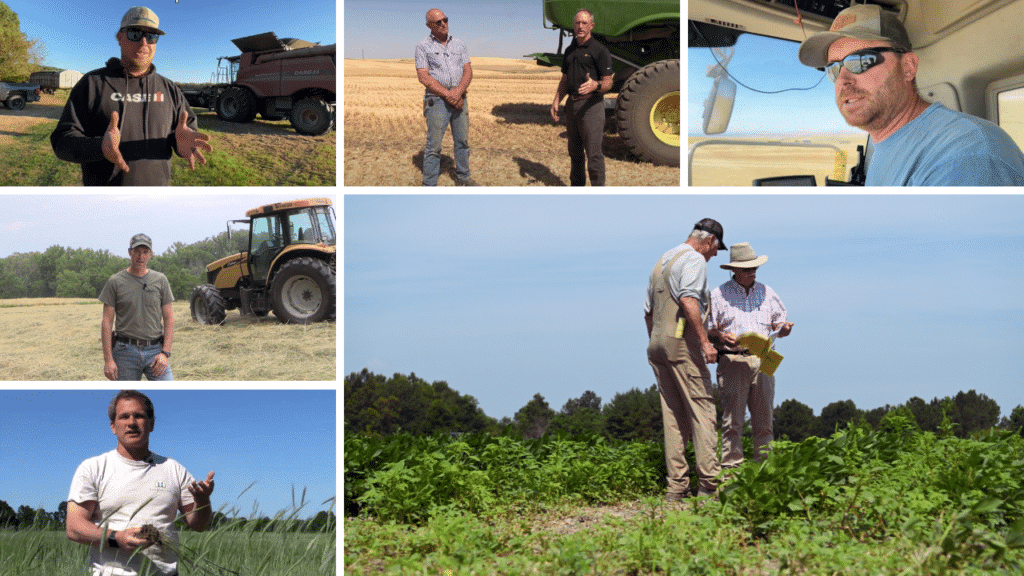
Learn from the Best: GROW Farmer Case Studies
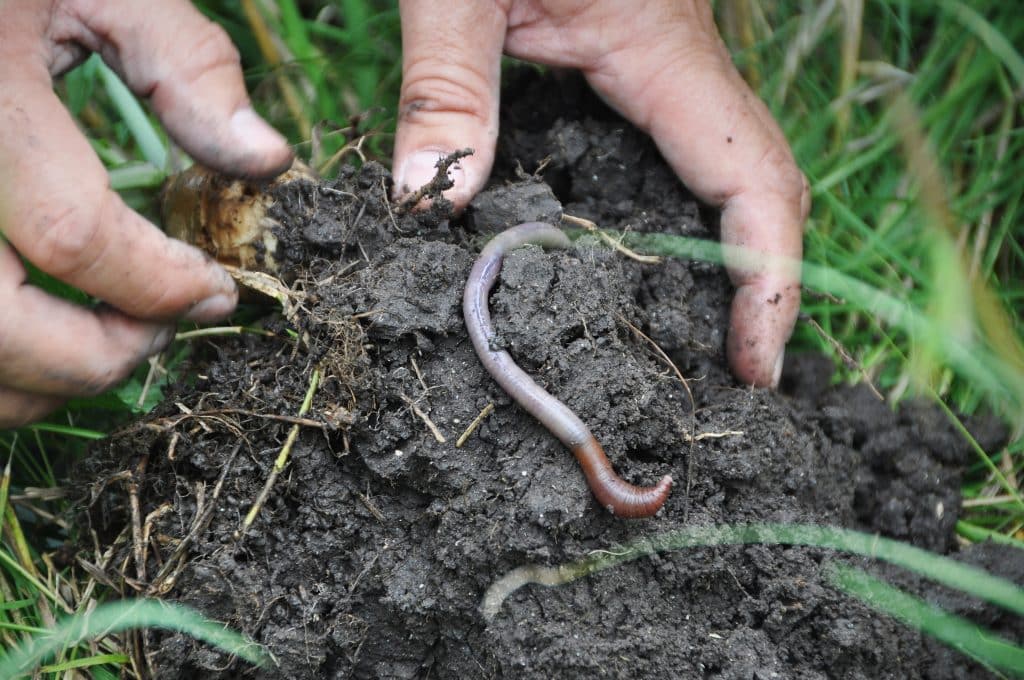
After the Volts: Is Weed Electrocution Safe for the Soil?

Mowing, Zapping, and Outcompeting Weeds: Opportunities and Trade-Offs
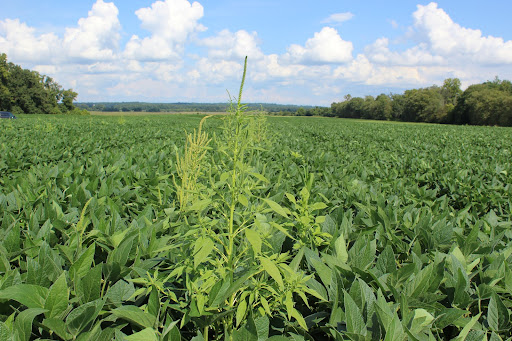
How to Manage Weeds in the Face of Regulation and Resistance
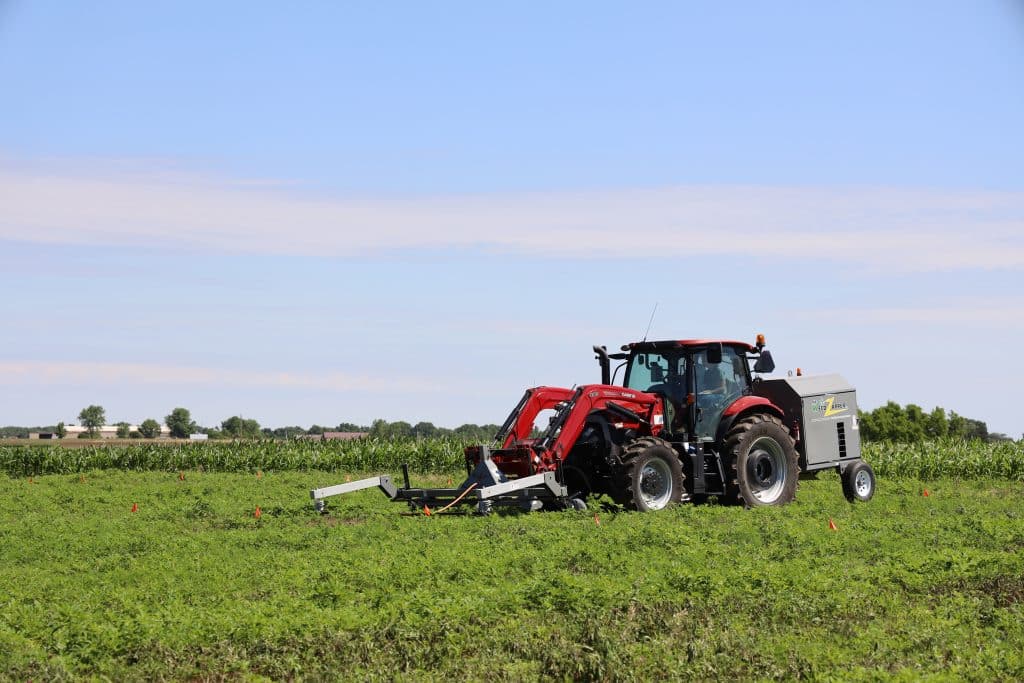
Missouri Scientists Explore Weed Electrocution in Soybeans
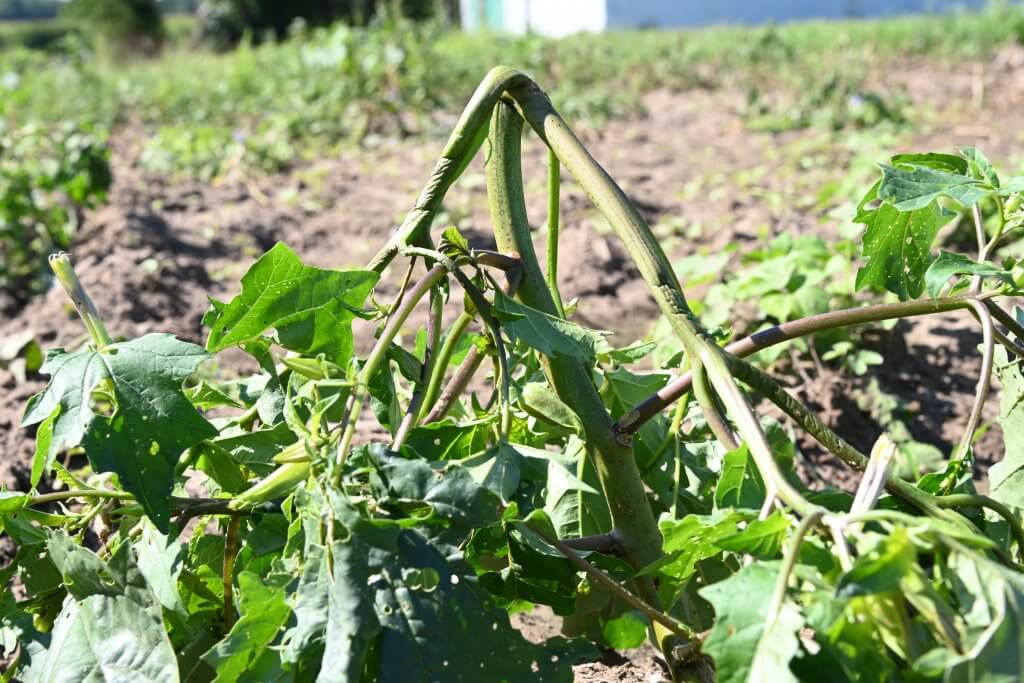
How One Farmer Is Using Weed Electrocution
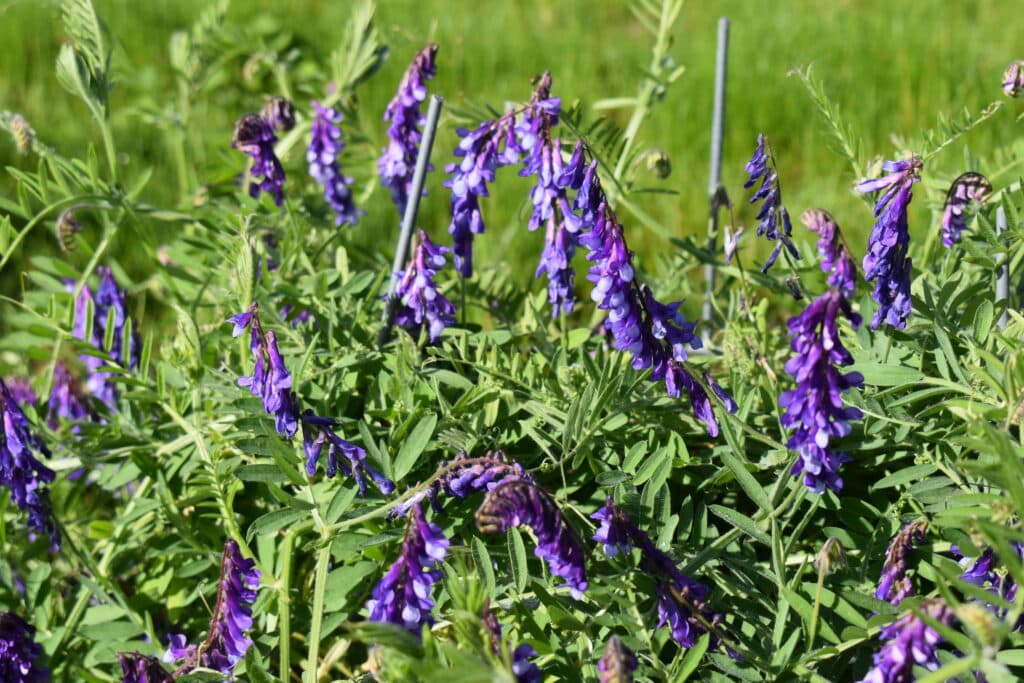
Research Unveils the Secret Life of Hairy Vetch — And How to Change It
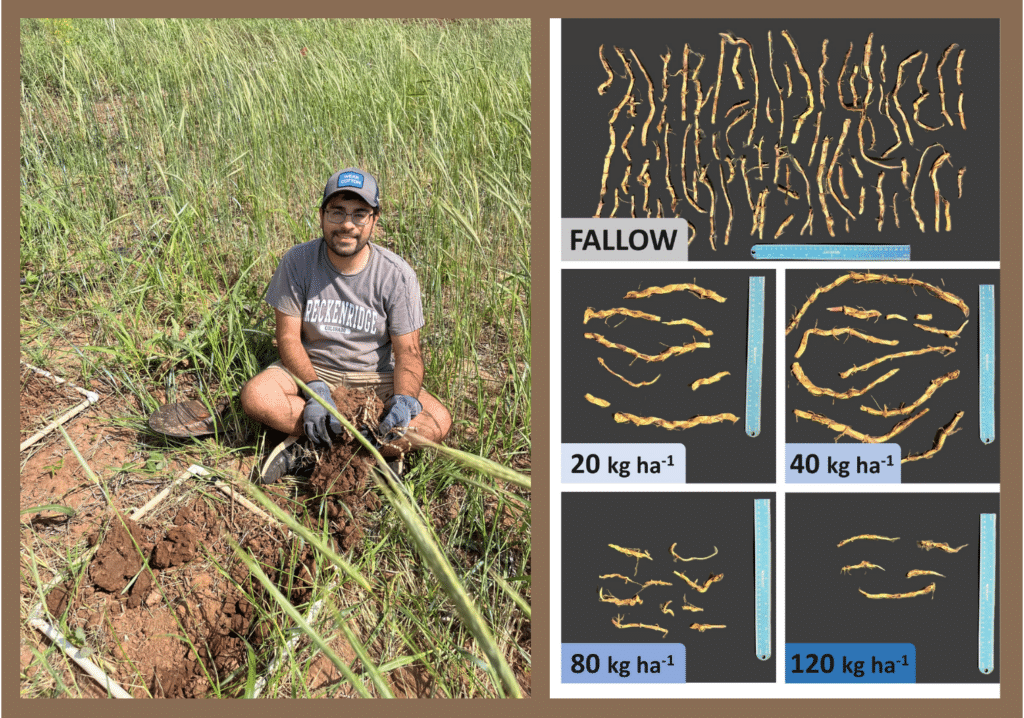
Underground Warfare: Cereal Rye Cover Crop Suppresses Johnsongrass Rhizomes
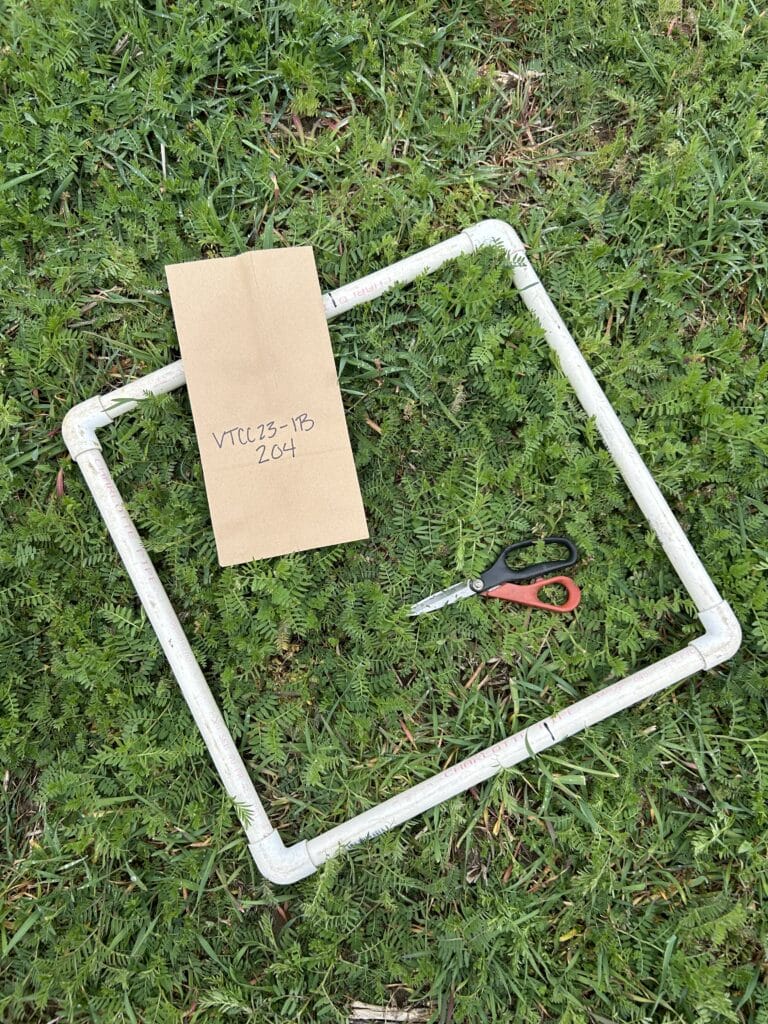
Mix Cereal Rye with Hairy Vetch to Cash In on Cover Crop Benefits
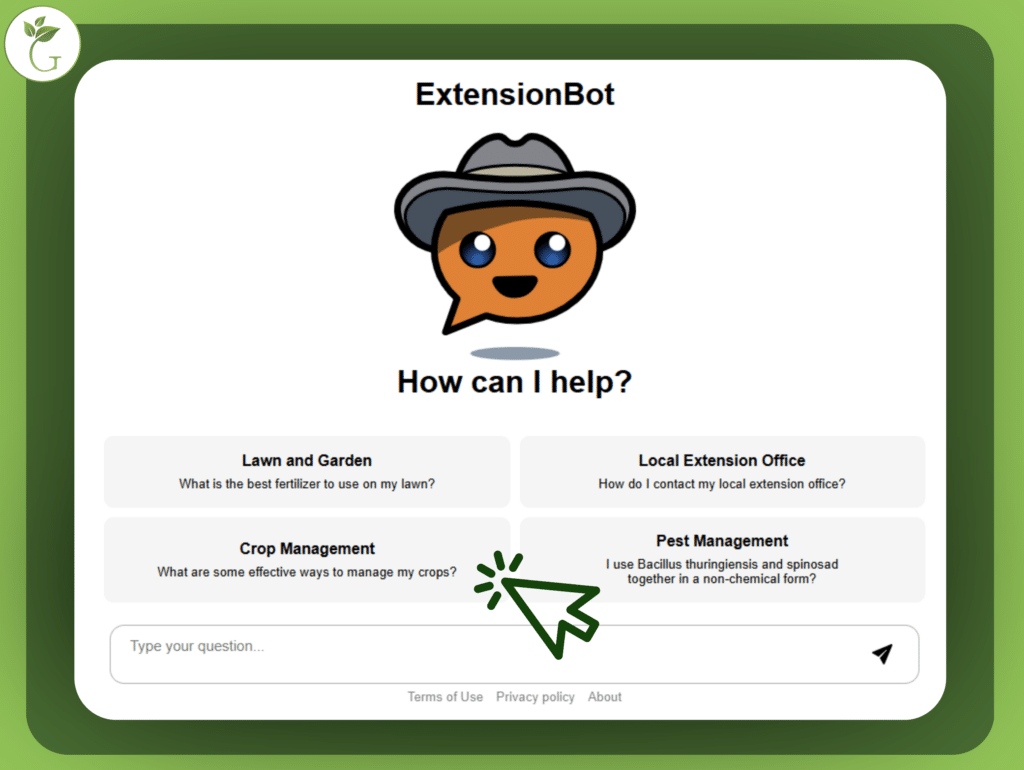
A Handheld Extension Agent? GROW Researchers Put ExtensionBot to the Test
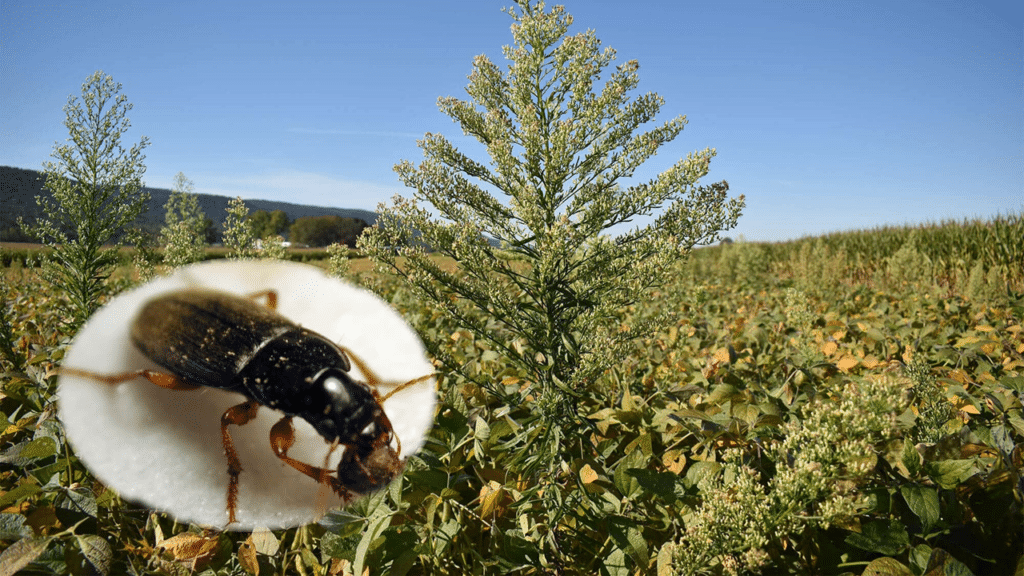
Insecticides May Contribute to Bigger Problems with Certain Weeds
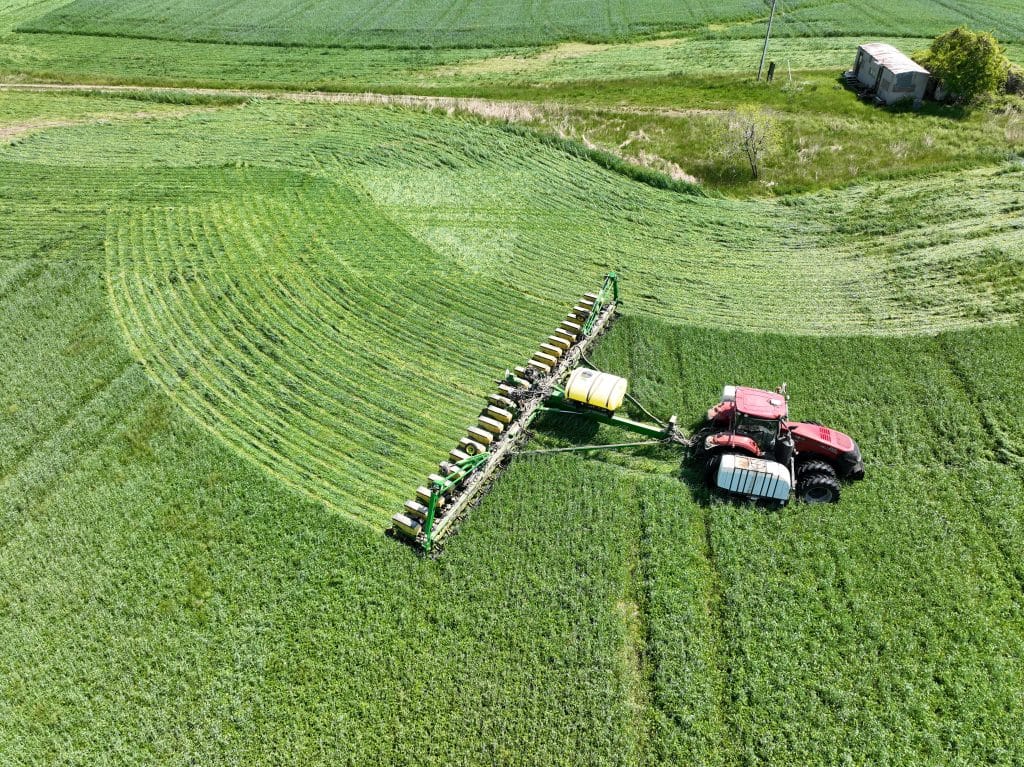
The Lowdown on Roller Crimpers
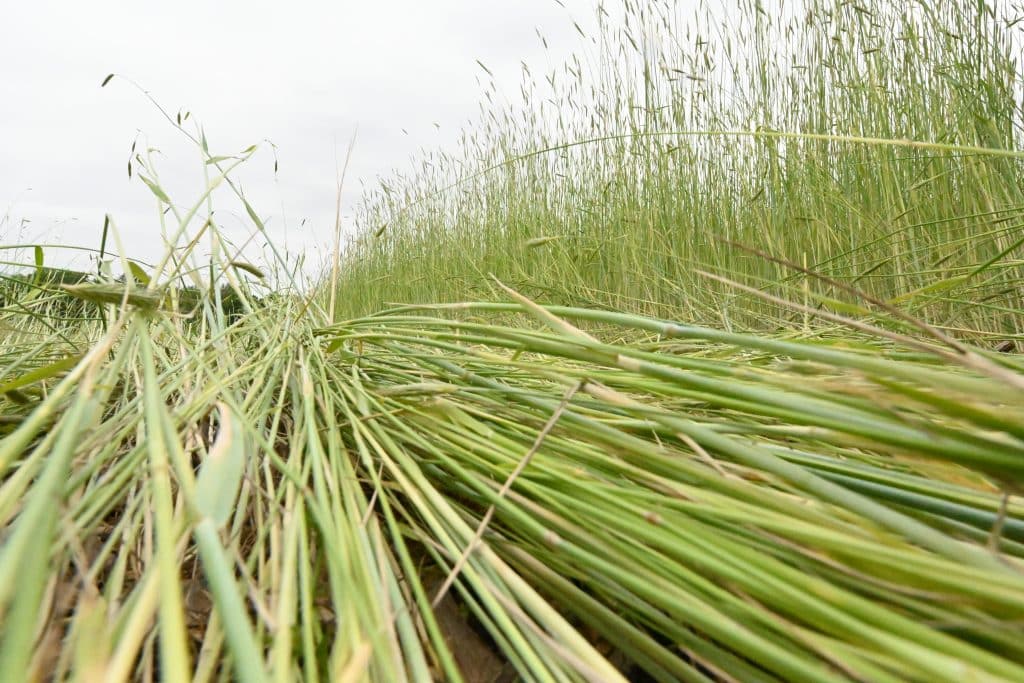
Farmer Forum Recap: Cover Crop Termination
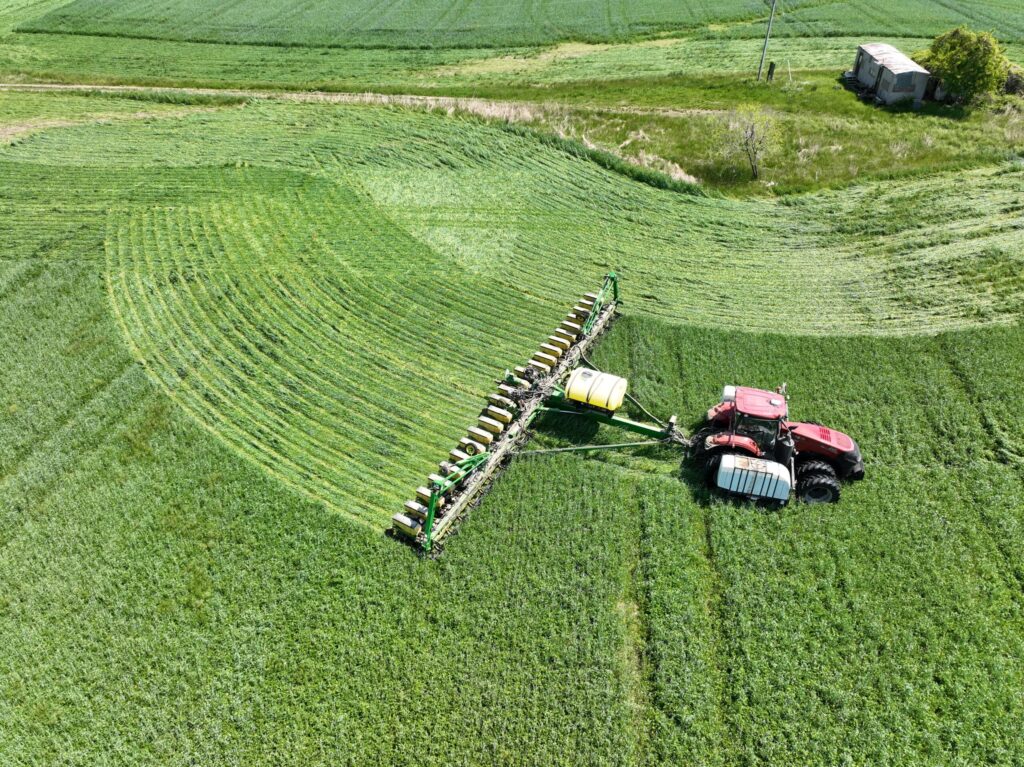
Squash Pigweeds With These Cover Crop Management Strategies
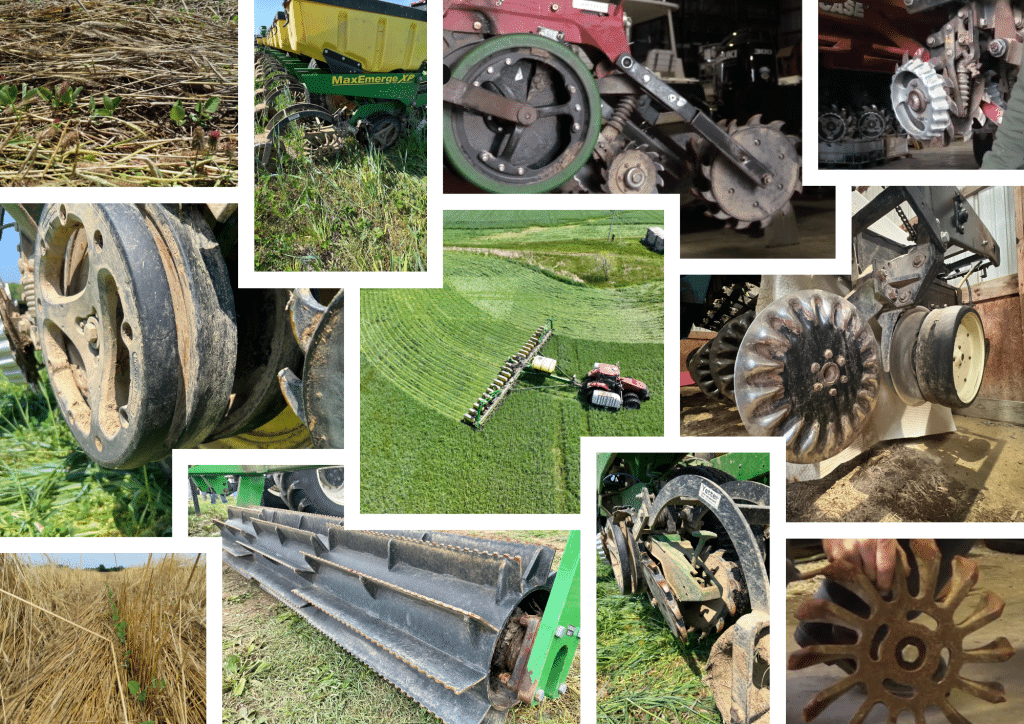
A Look at Planter Adjustments for Planting into Cover Crops
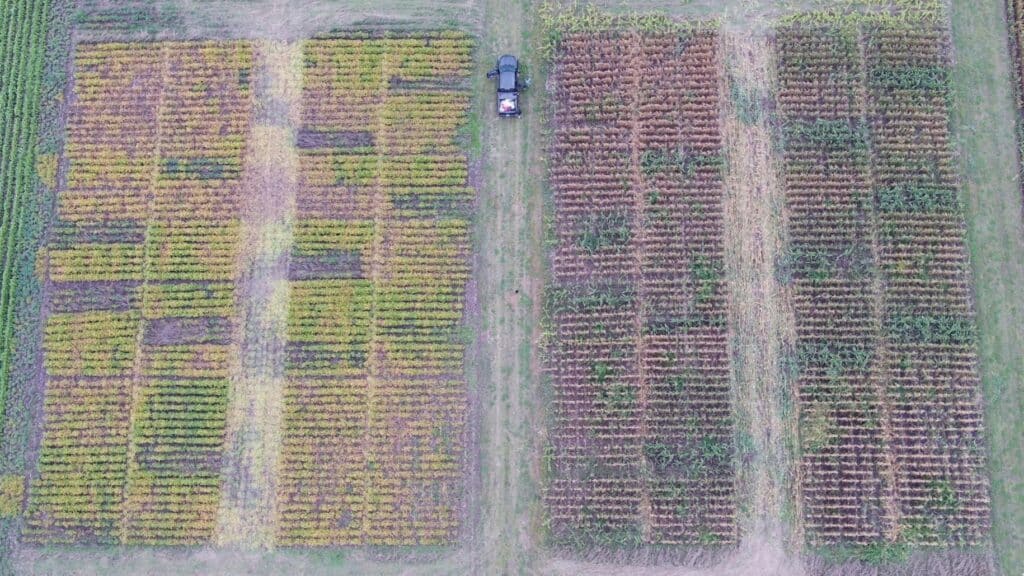
How to Manage Cereal Rye in the Upper Midwest for Weed Suppression and Max Yields
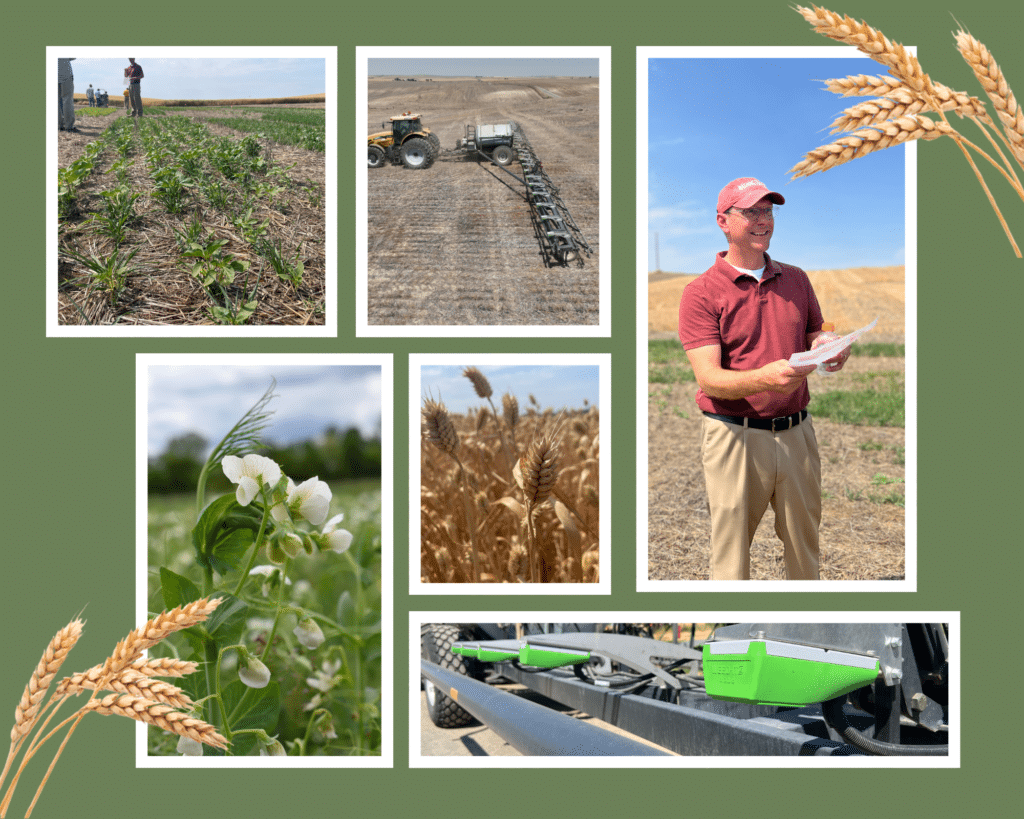
All-of-the-Above Management: Weed Control in Organic Grain Production in the Pacific Northwest

Weed Management Planner: Order Your Free Prints Now!
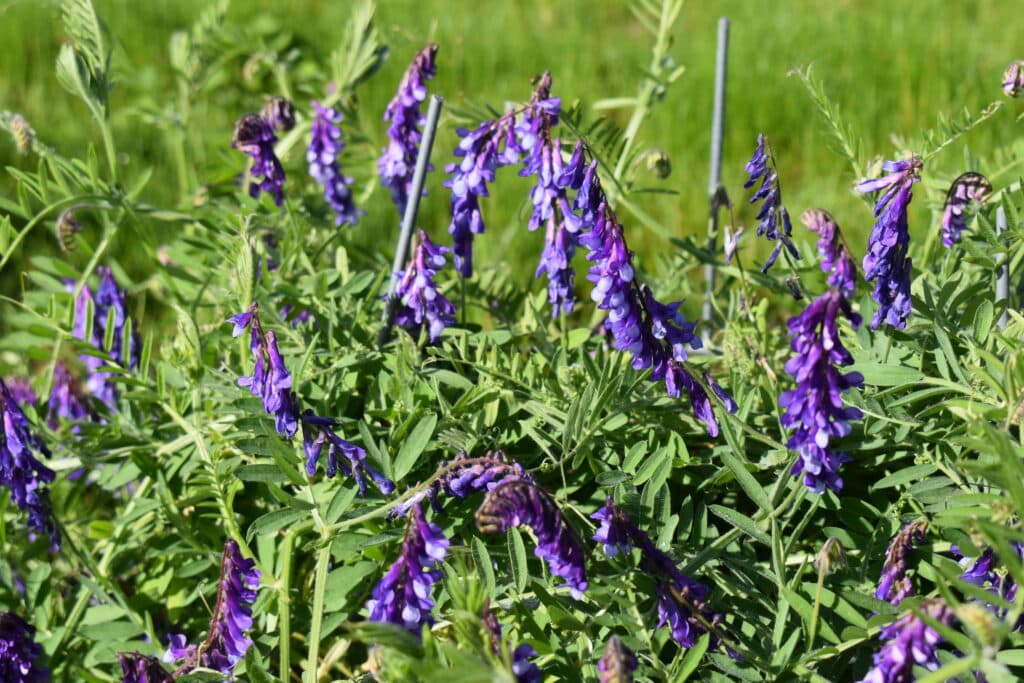
Research Unveils the Secret Life of Hairy Vetch — And How to Change It
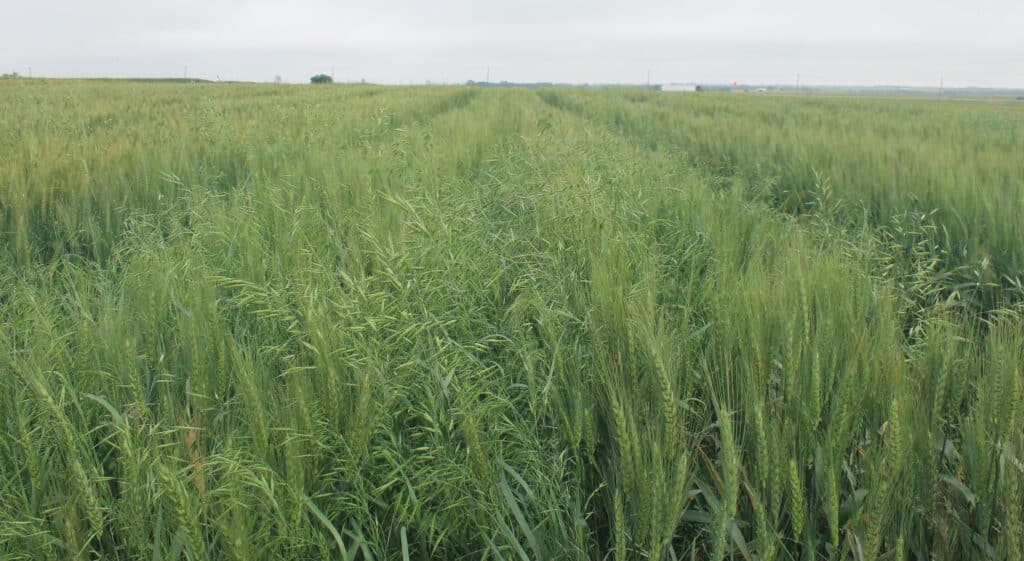
Fight Weeds with Time: Delay Winter Wheat Planting to Manage Cheat and Downy Brome
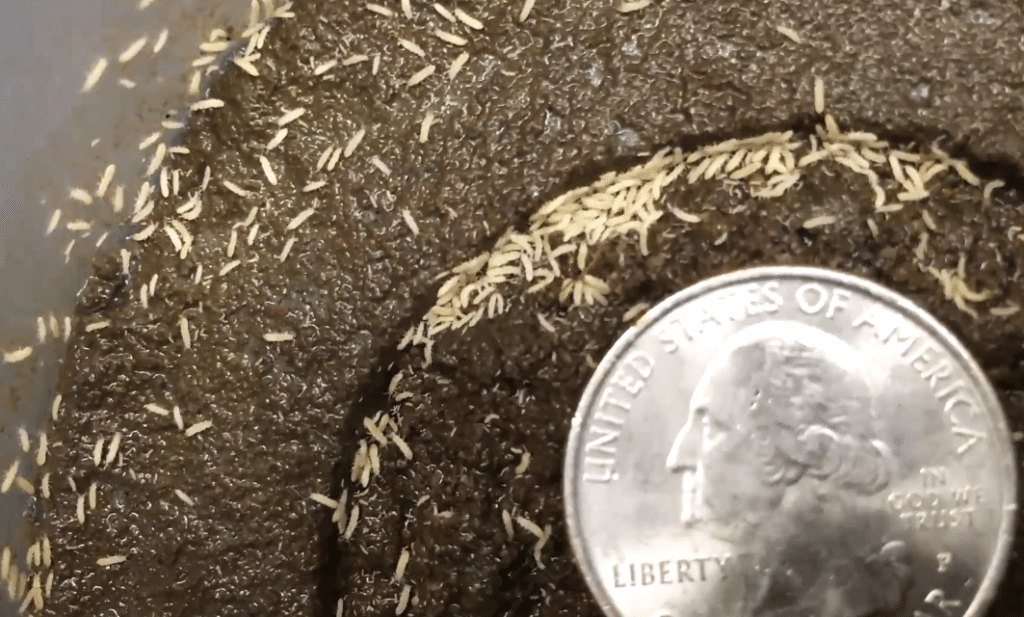
Underground Army: How Soil Invertebrates May Help Farmers Manage Weeds
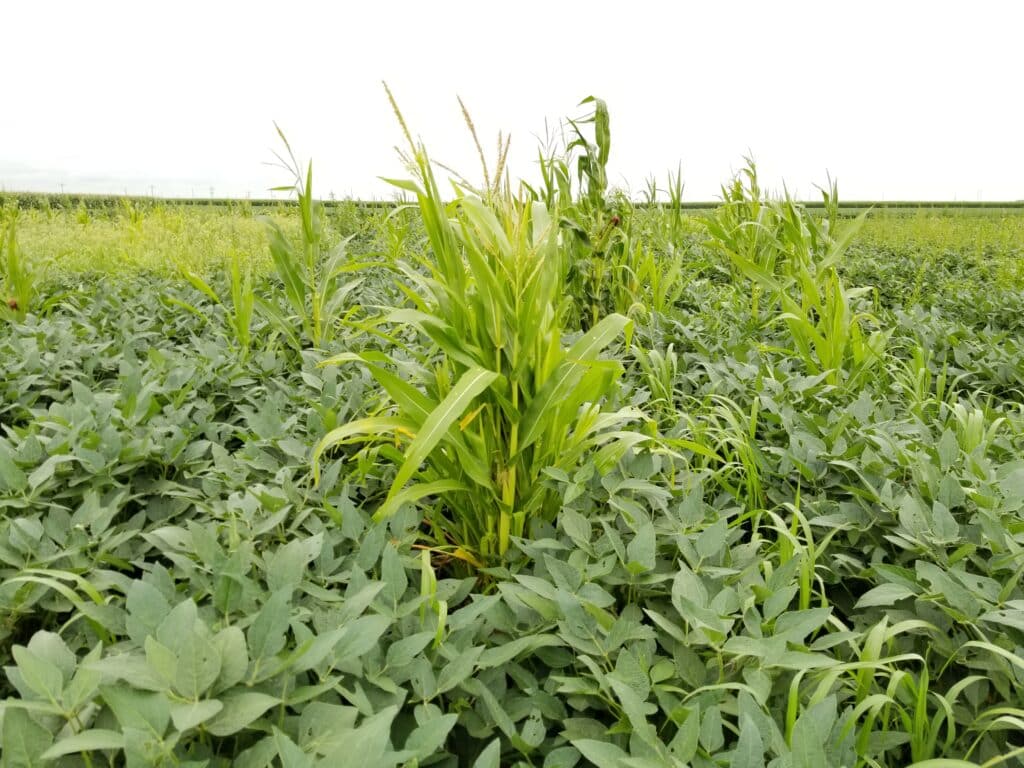
Unwanted Volunteers: How Much Corn Are You Losing at Harvest?
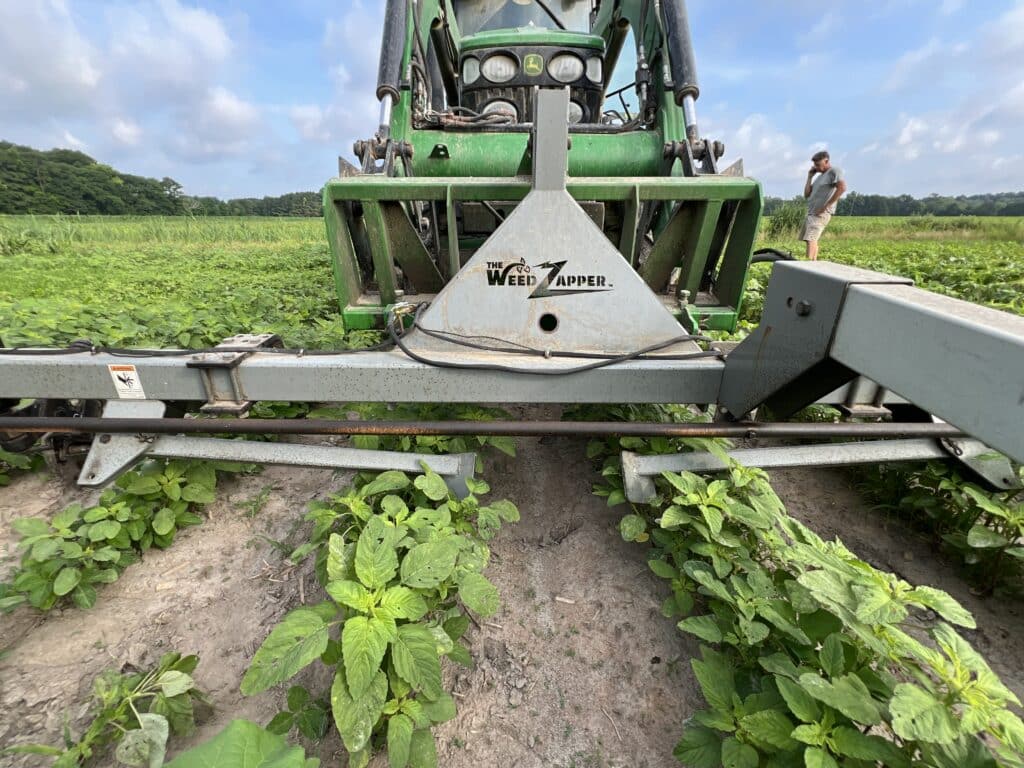
Join a GROW Farmer Forum on Weed Electrocution in the Field
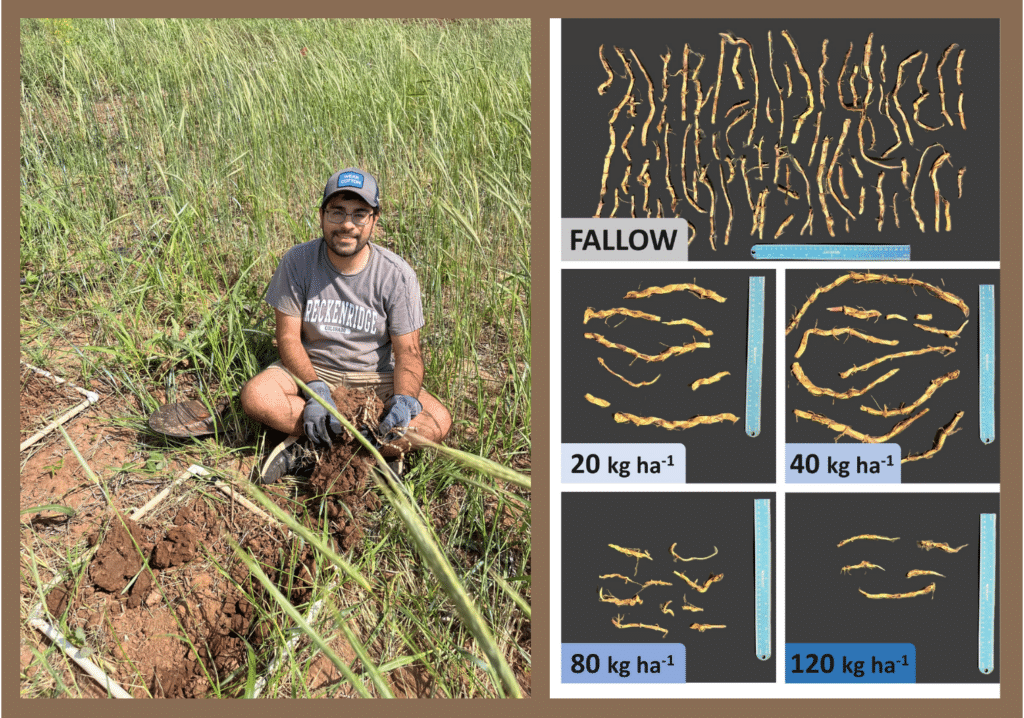
Underground Warfare: Cereal Rye Cover Crop Suppresses Johnsongrass Rhizomes
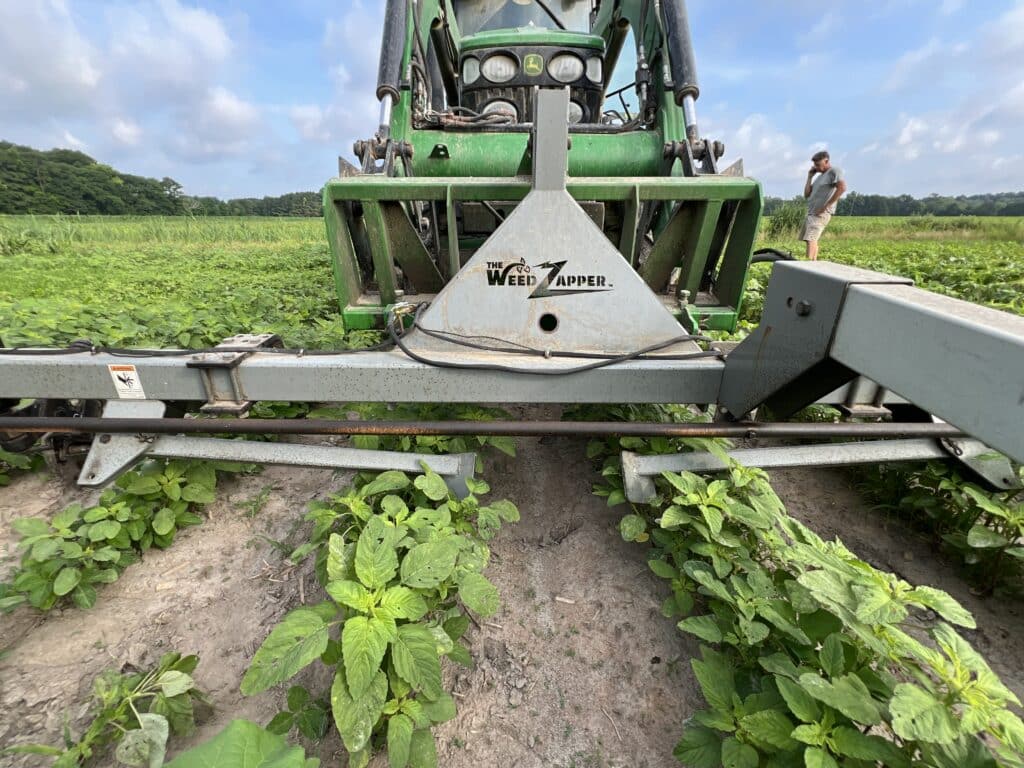
Join a GROW Farmer Forum on Weed Electrocution in the Field
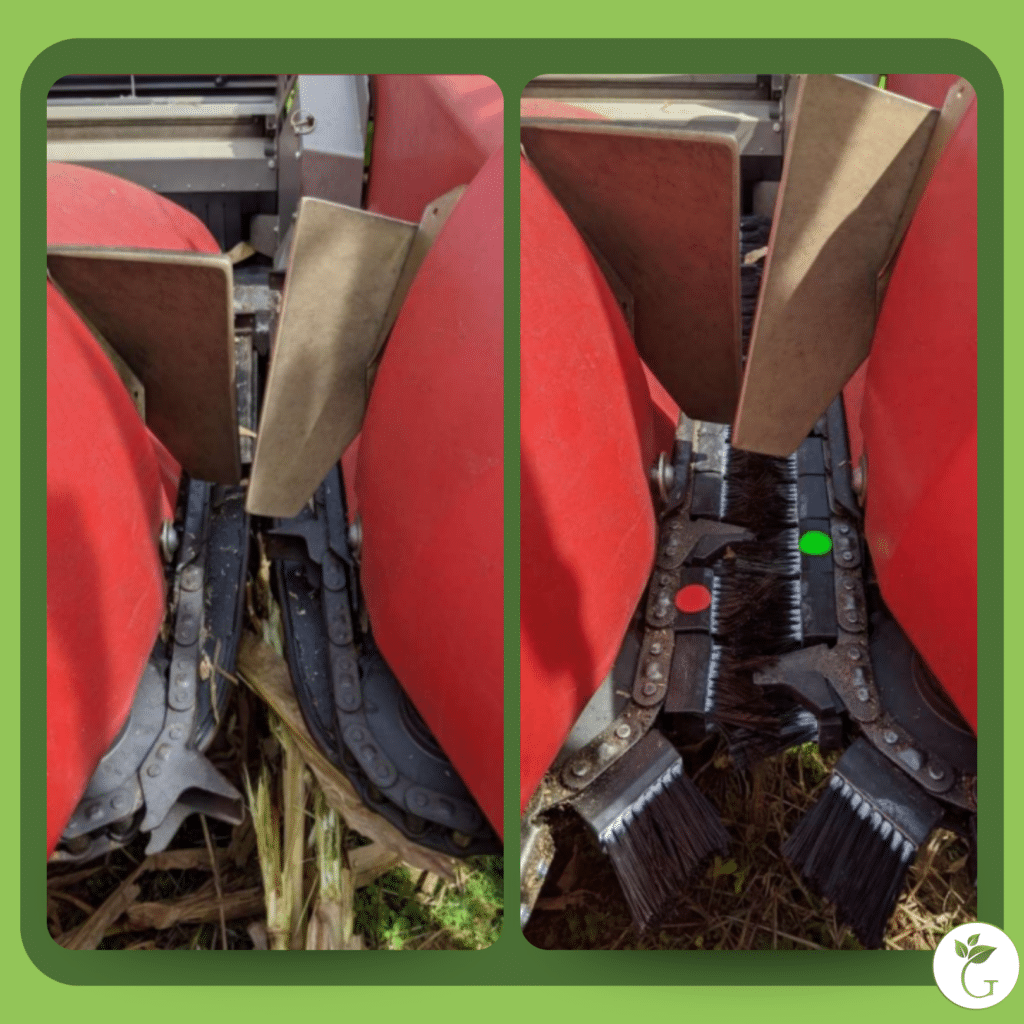
This Harvest Device Catches Corn Kernels and Weed Seeds
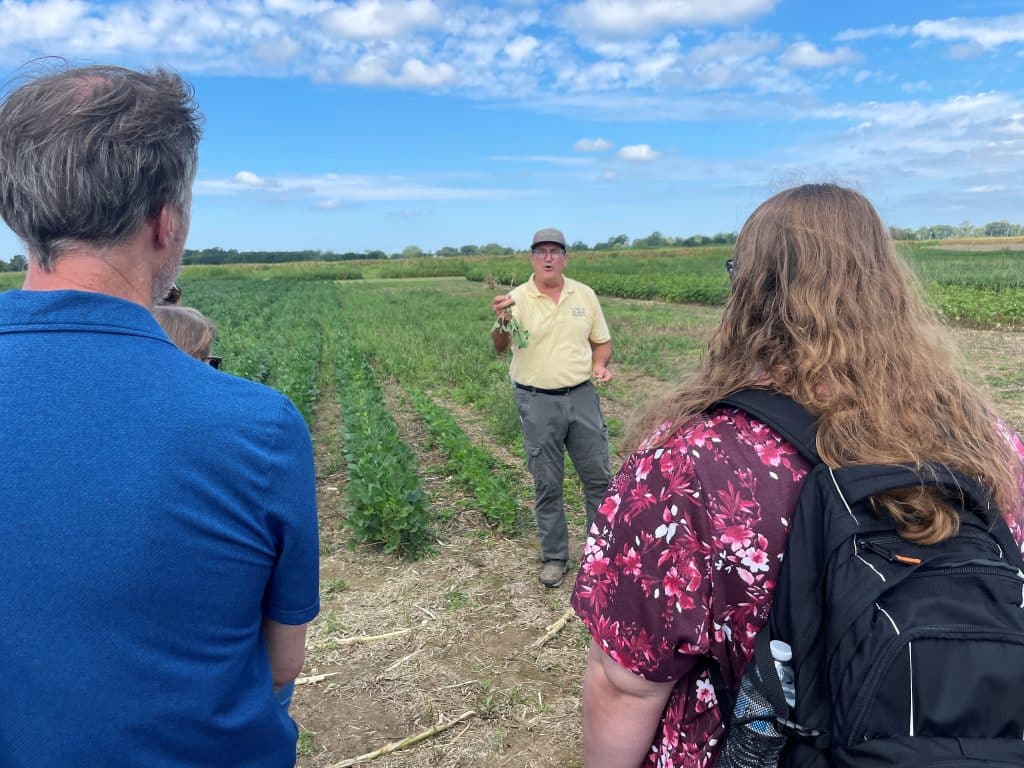
Weed Science Field Days: What’s In It For Me?
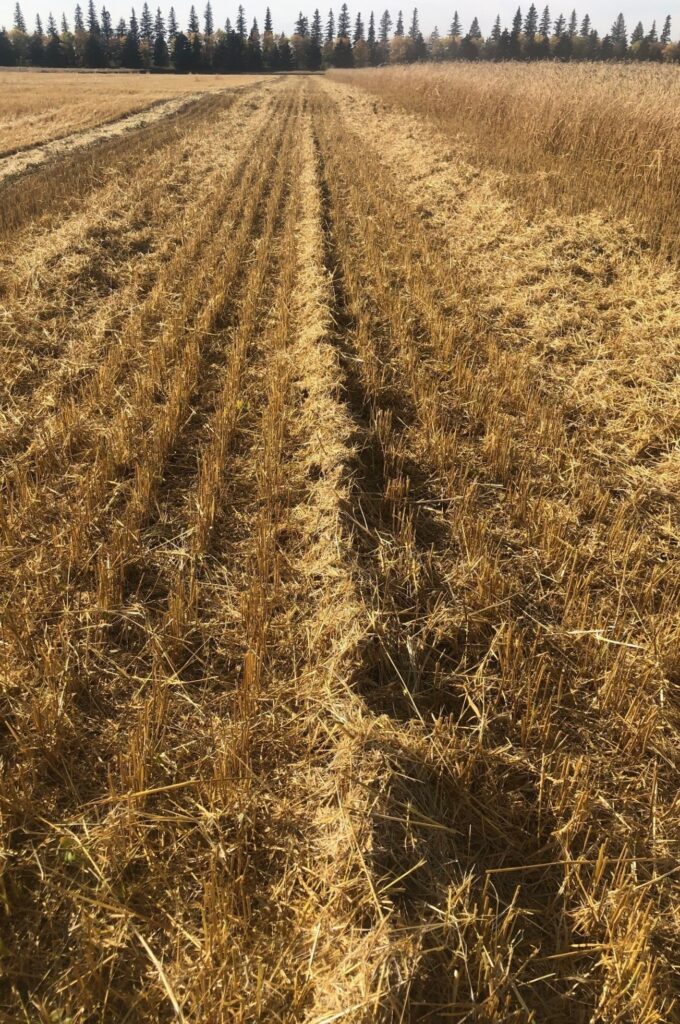
Can Chaff Lining Cut Costs and Corral Weeds in the Canadian Prairies?
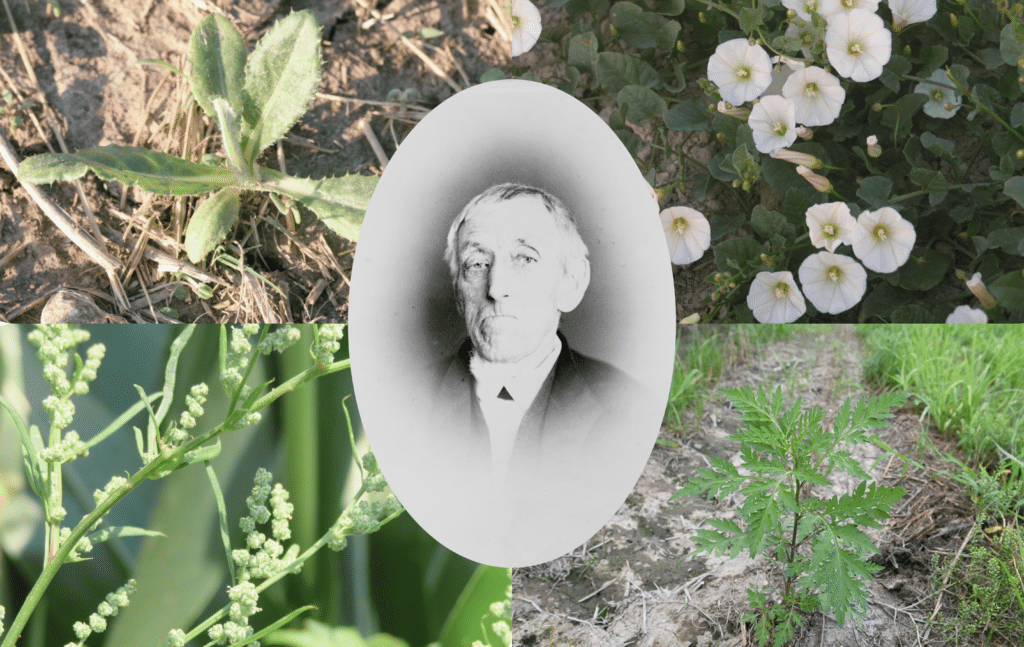
Fighting Weeds in 1872: A Trip Back in Time to the First Weed Management Guide
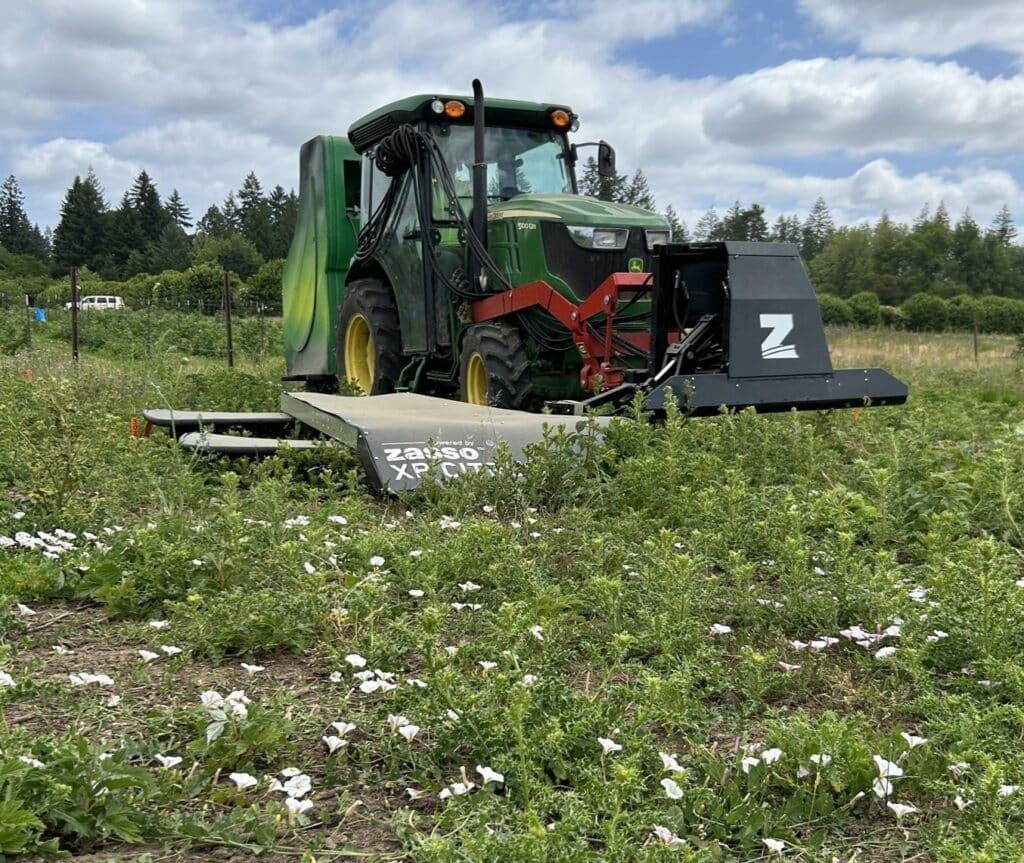
Slow the Cycle: Targeting Perennial Weeds with Weed Electrocution
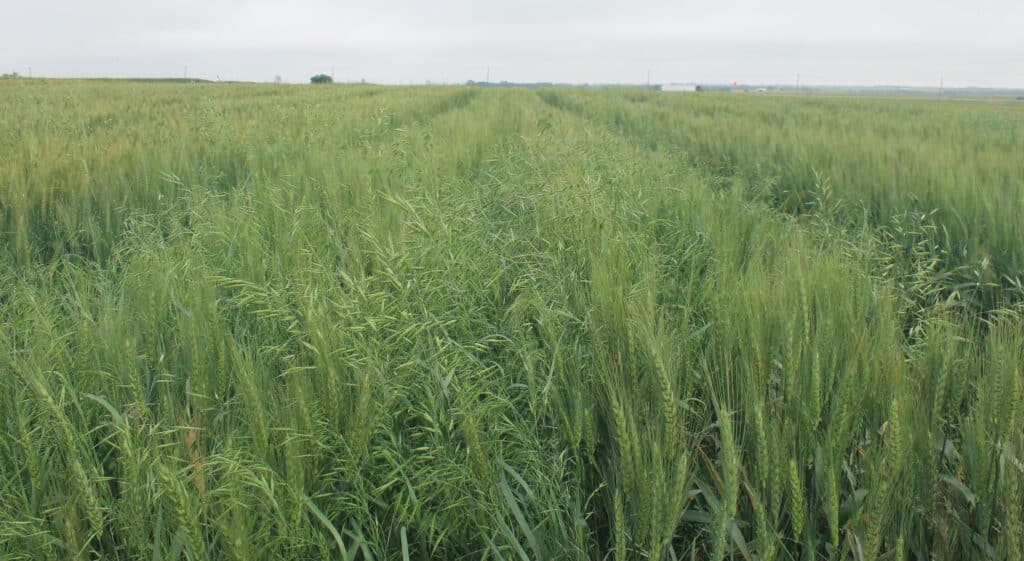
Fight Weeds with Time: Delay Winter Wheat Planting to Manage Cheat and Downy Brome
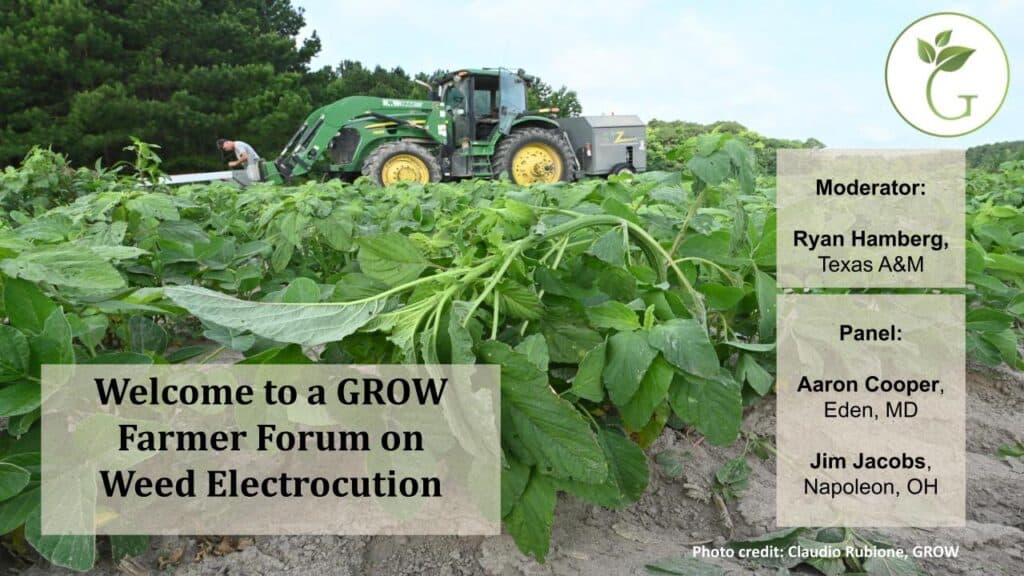
Farmer Forum Recap: Weed Electrocution in the Field
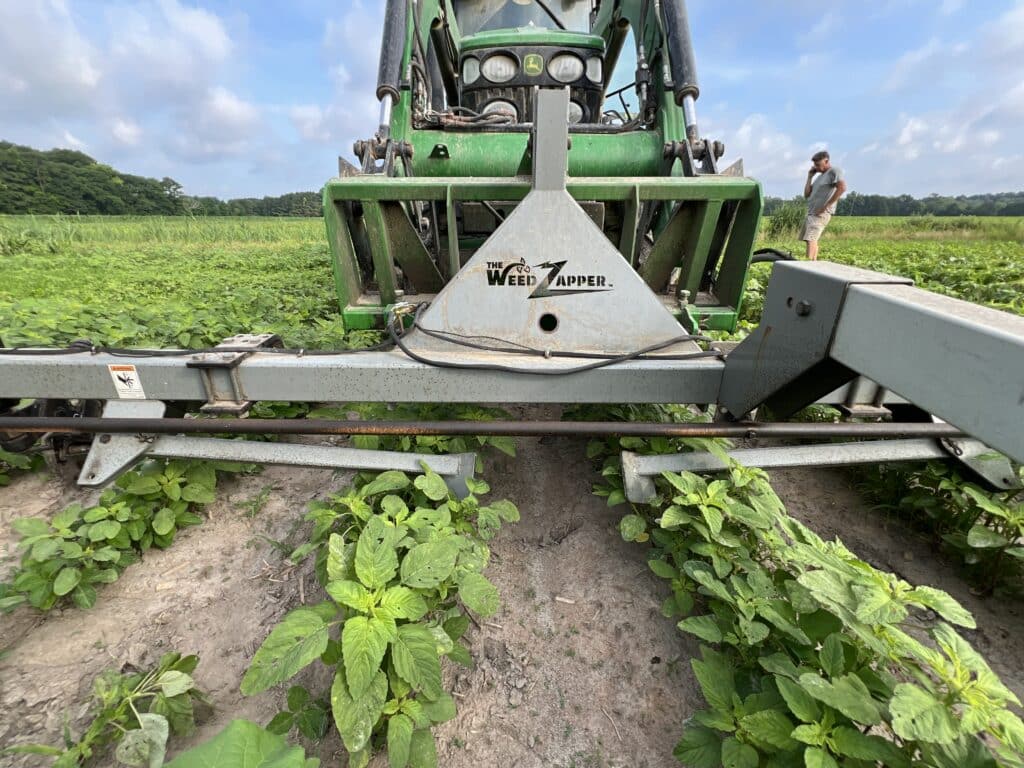
Join a GROW Farmer Forum on Weed Electrocution in the Field
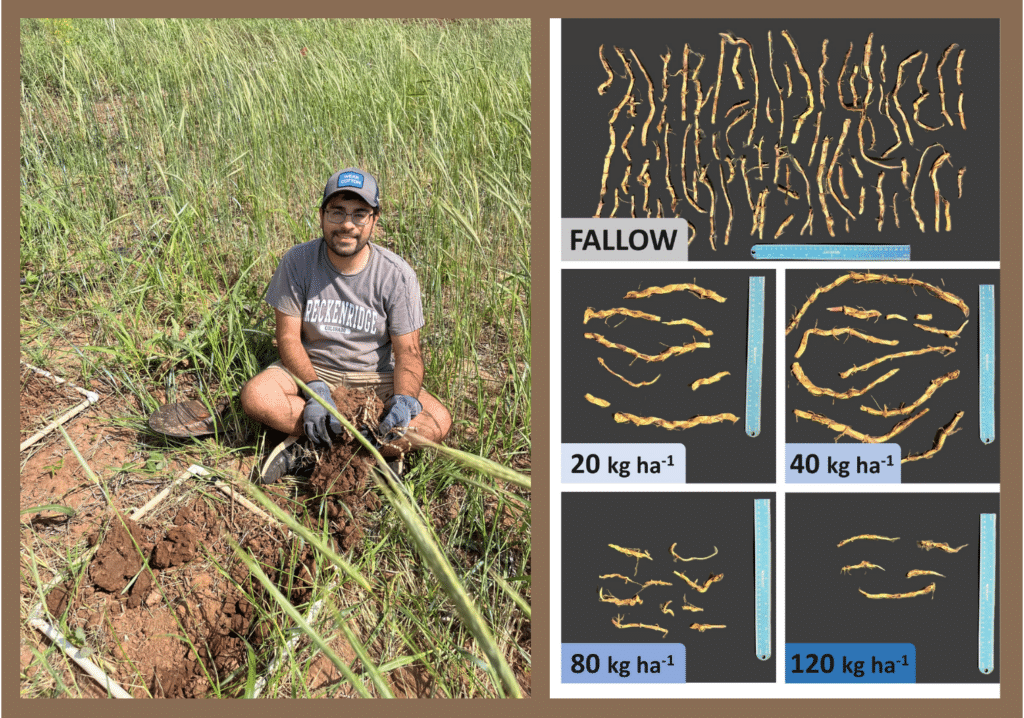
Underground Warfare: Cereal Rye Cover Crop Suppresses Johnsongrass Rhizomes
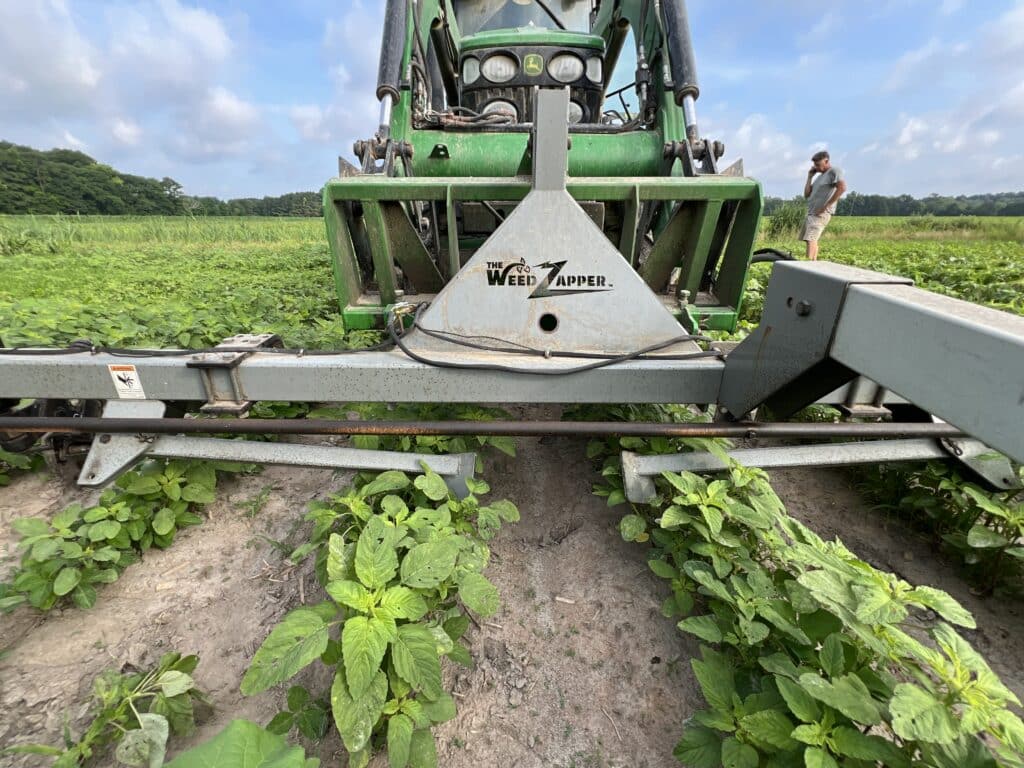
Join a GROW Farmer Forum on Weed Electrocution in the Field
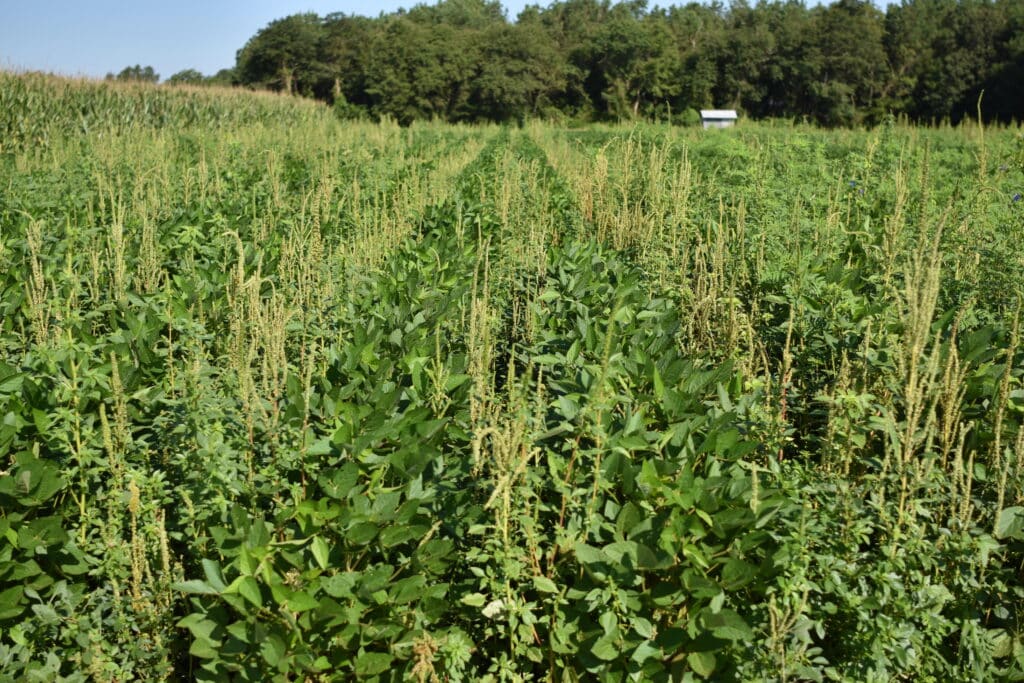
MSU-Led Multi-State Research Team Receives $500K Grant to Combat Herbicide-Resistant Weeds in Soybeans
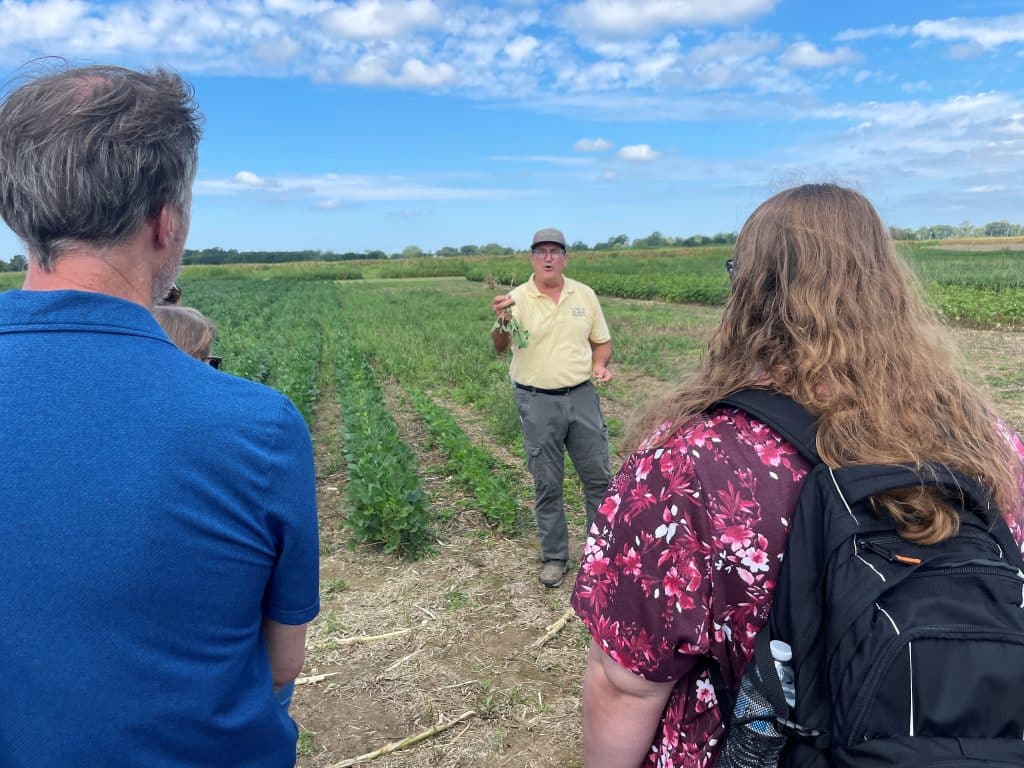
Weed Science Field Days: What’s In It For Me?
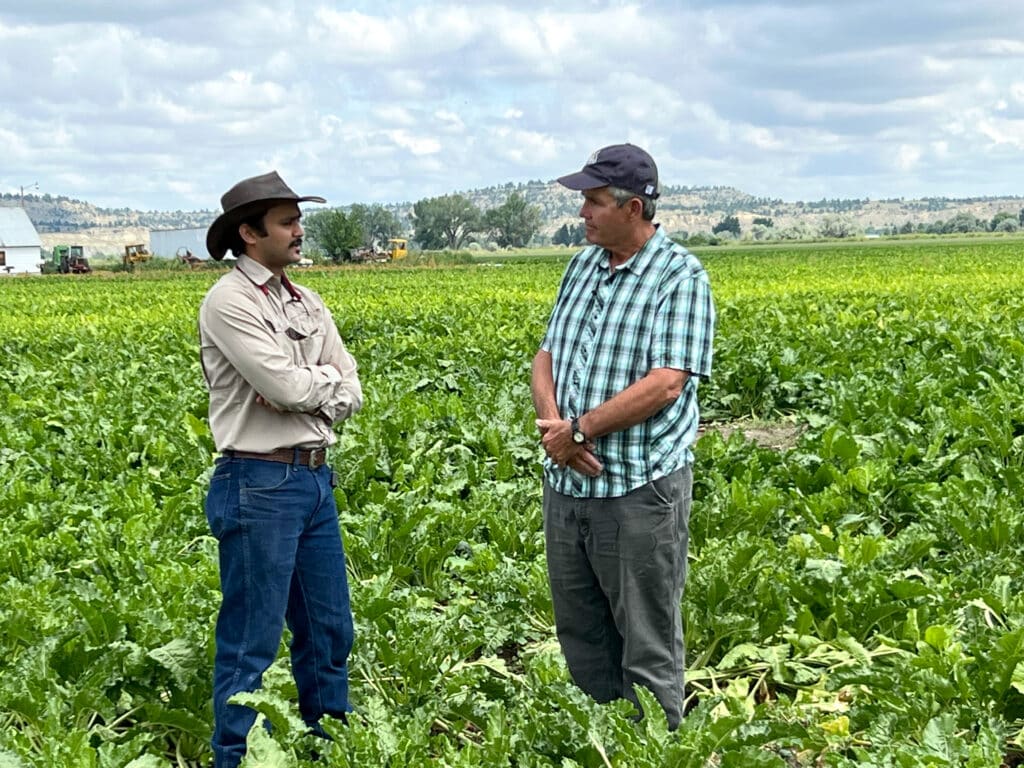
Triple-Stack Herbicide Trait in Sugarbeets Faces Resistance
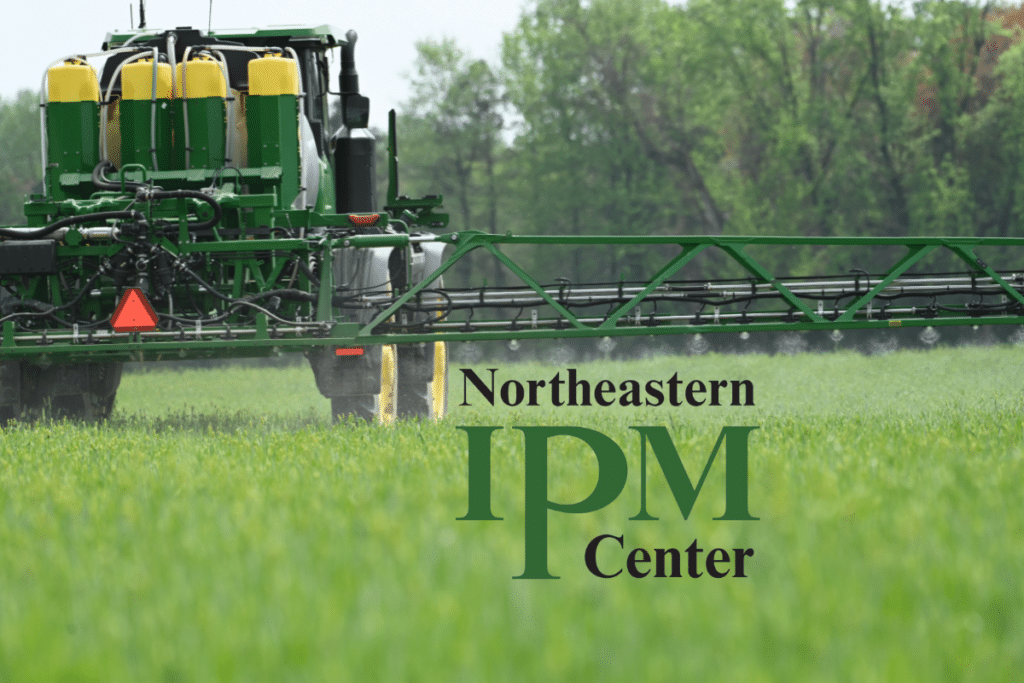
Pesticide Label Changes Brought On by the Endangered Species Act
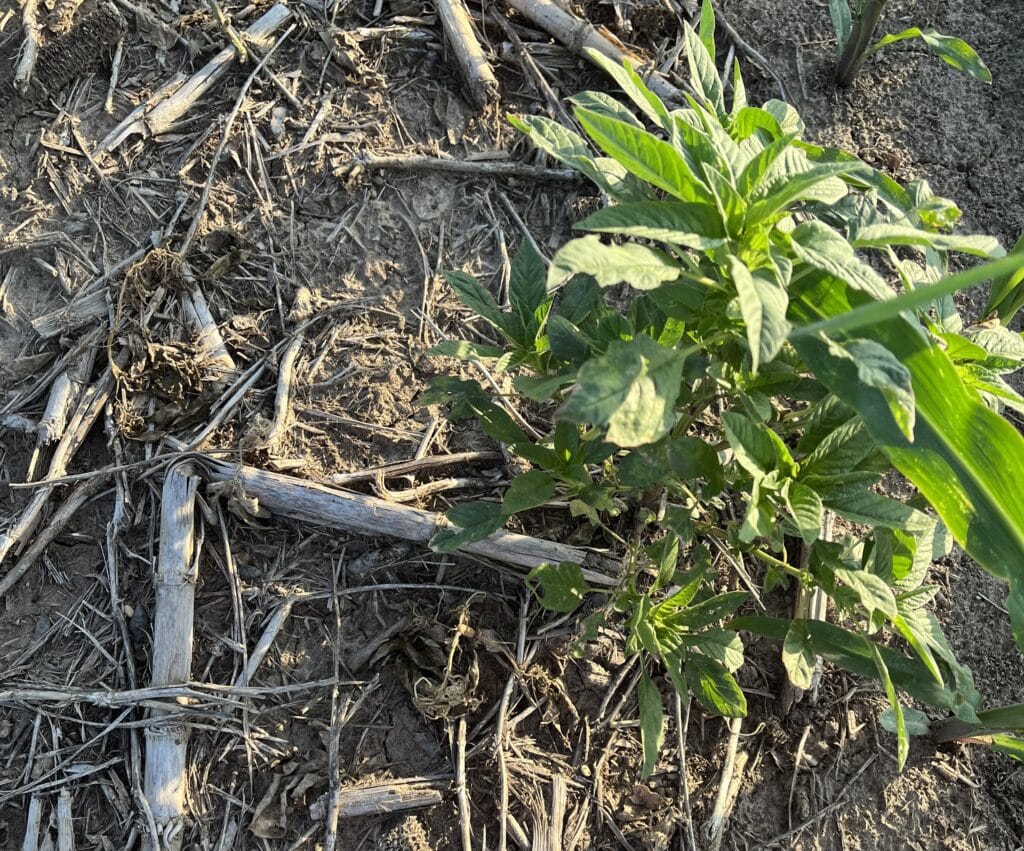
Keep These Tips in Mind When Using Target Sprayers
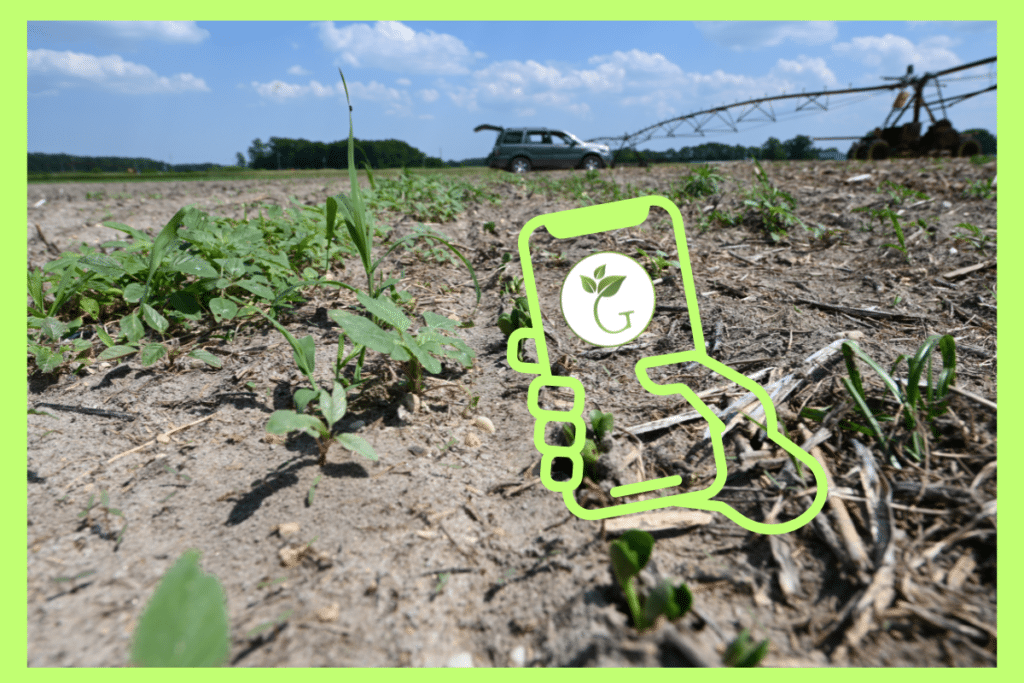
Heading to the Field to Scout? Take Us With You!
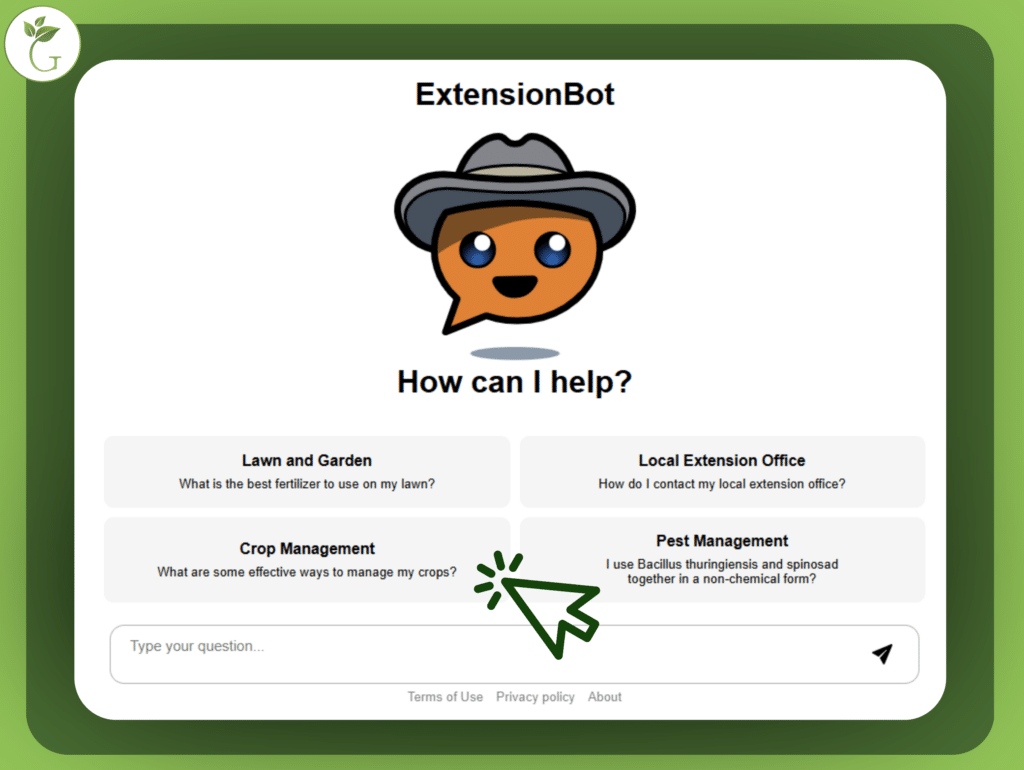
A Handheld Extension Agent? GROW Researchers Put ExtensionBot to the Test
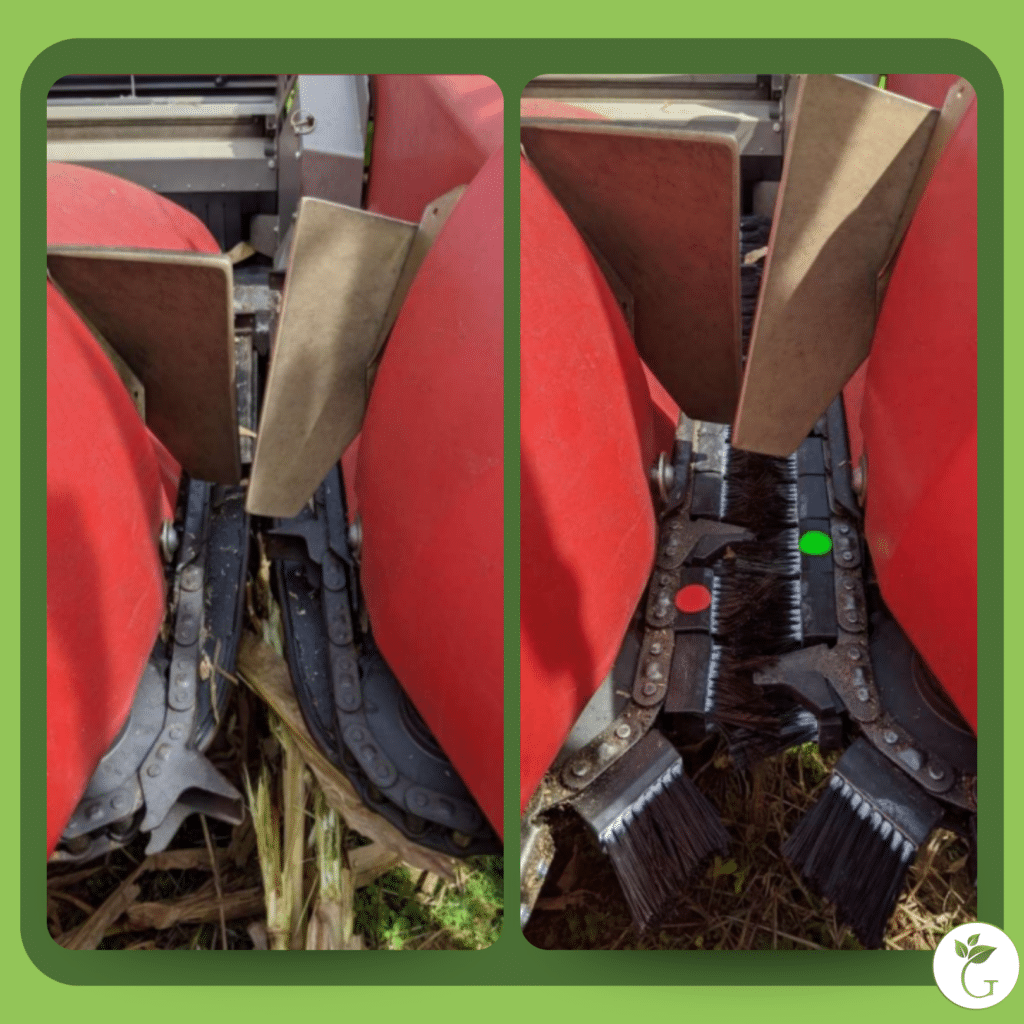
This Harvest Device Catches Corn Kernels and Weed Seeds
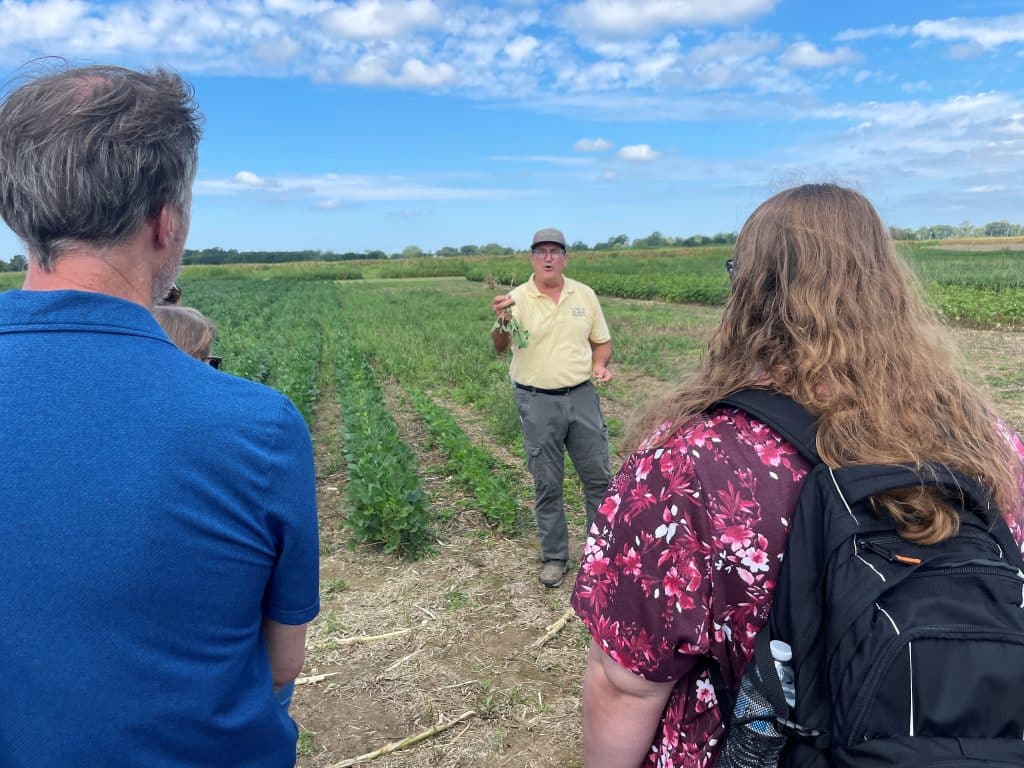
Weed Science Field Days: What’s In It For Me?
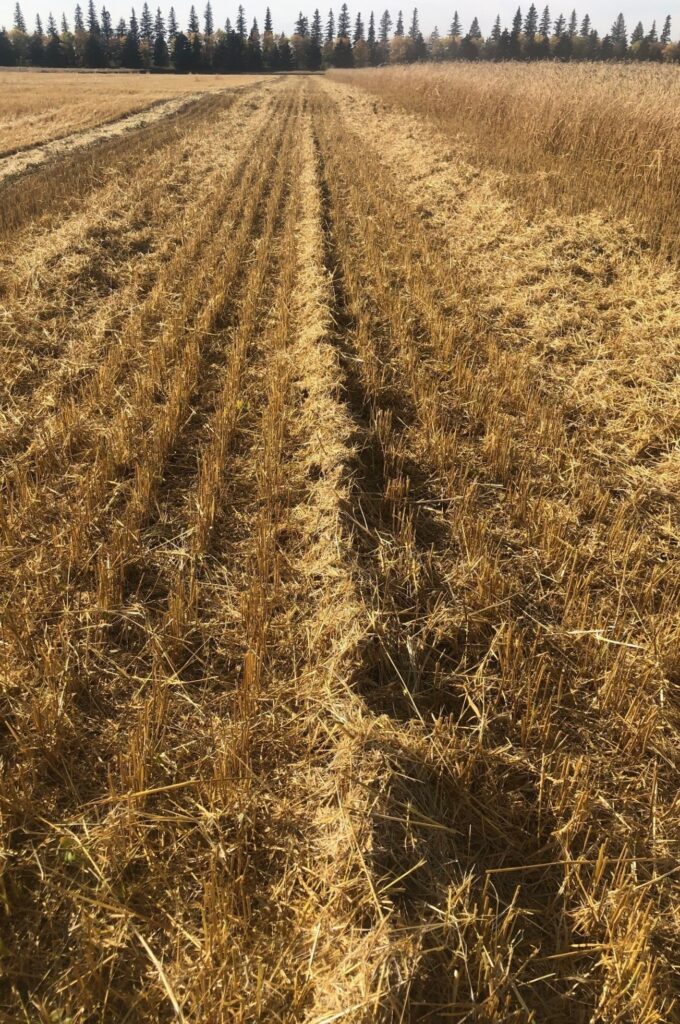
Can Chaff Lining Cut Costs and Corral Weeds in the Canadian Prairies?
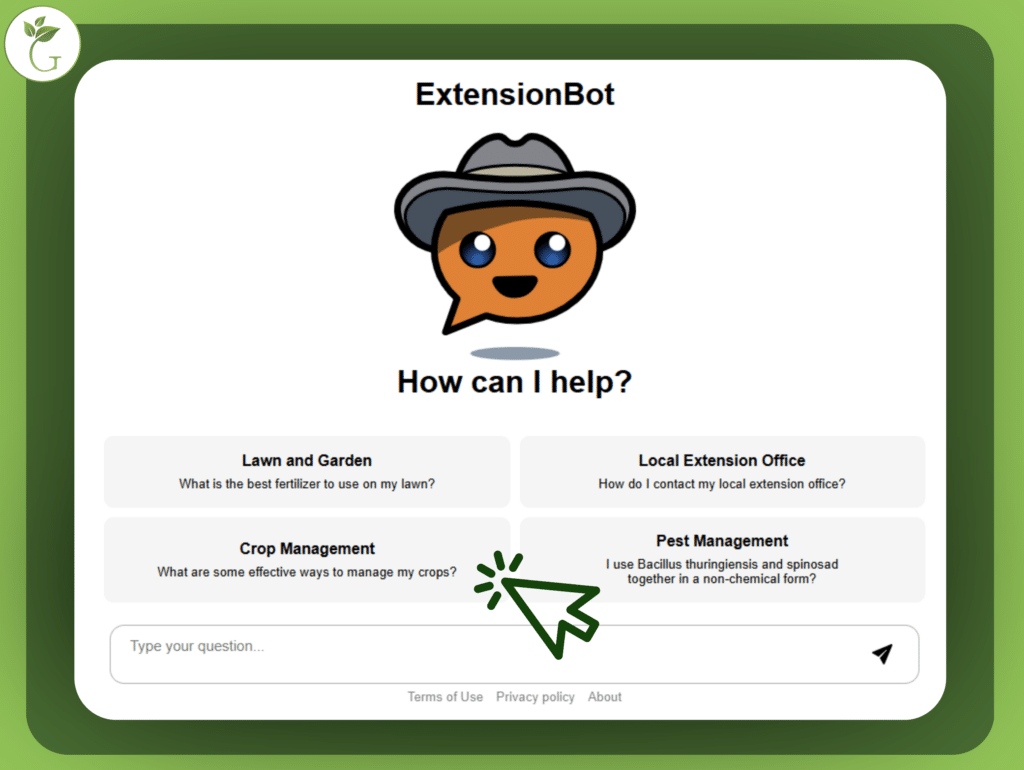
A Handheld Extension Agent? GROW Researchers Put ExtensionBot to the Test
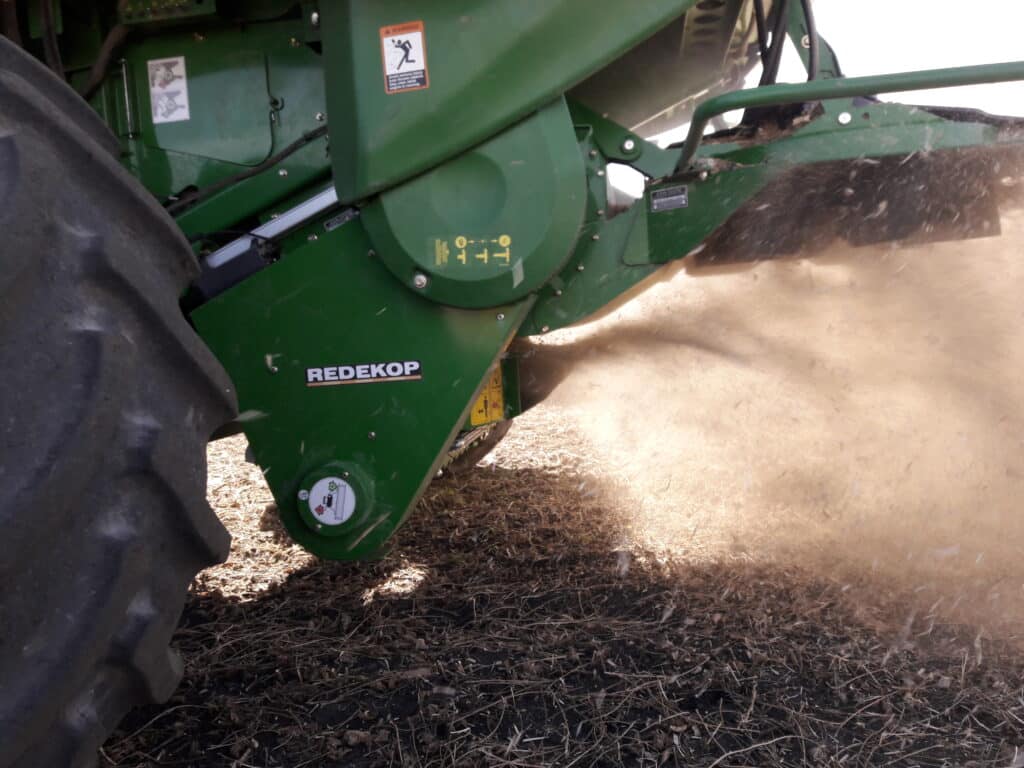
Seed Impact Mill Pulverizes Problematic Waterhemp in New Study

Weed Management Planner: Order Your Free Prints Now!
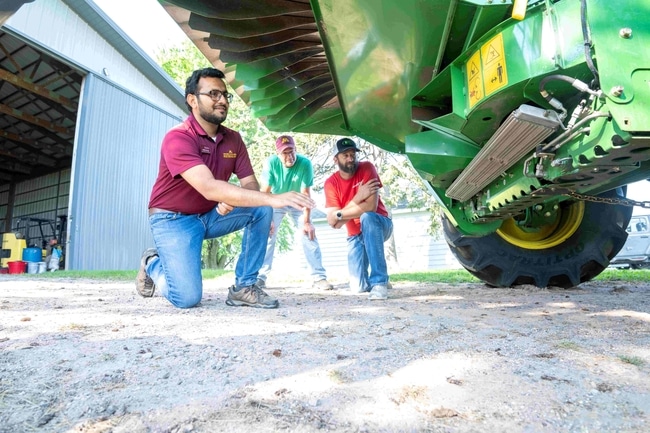
Extension and Farmers Greet Weed Control Option with ‘G’day’
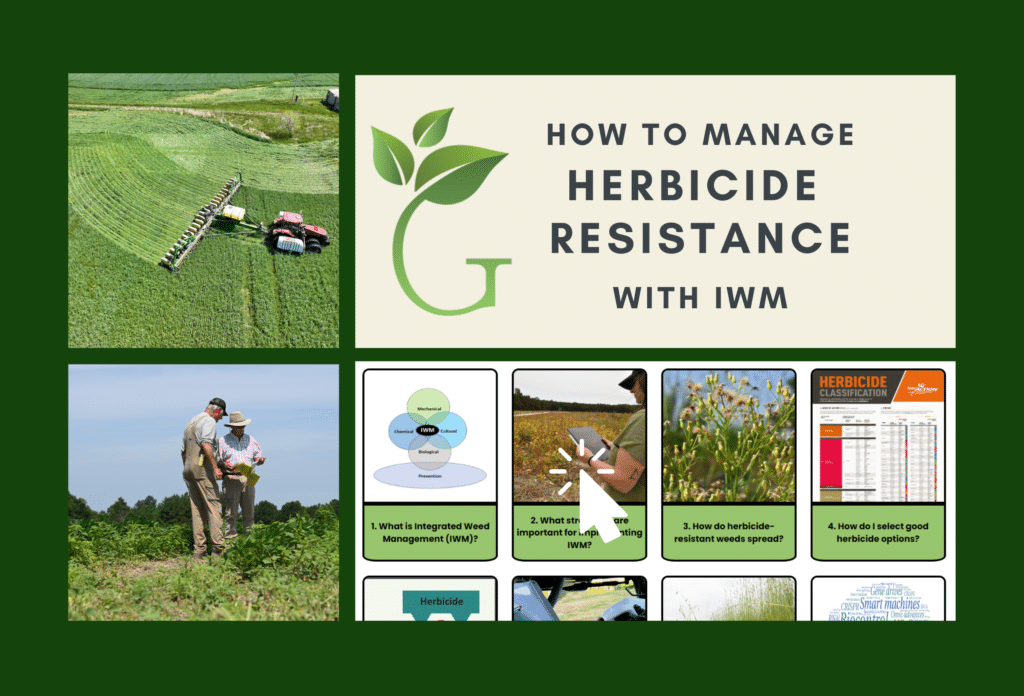
GROW Releases New Herbicide Resistance Resource for the Industry
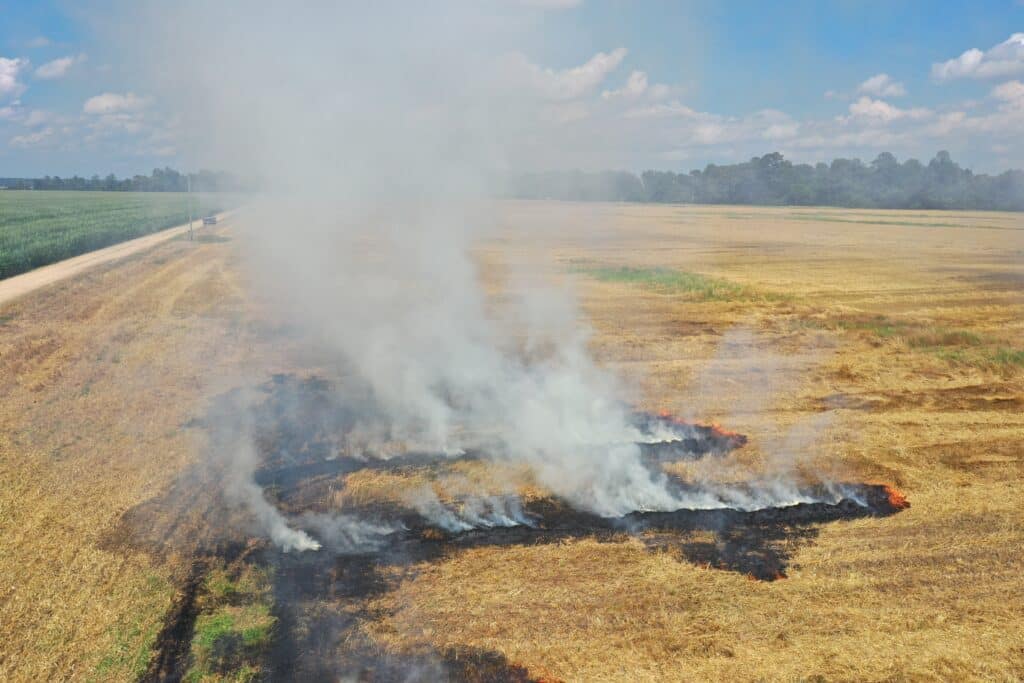
Narrow Windrow Burning for Weed Seed Control is Risky Business
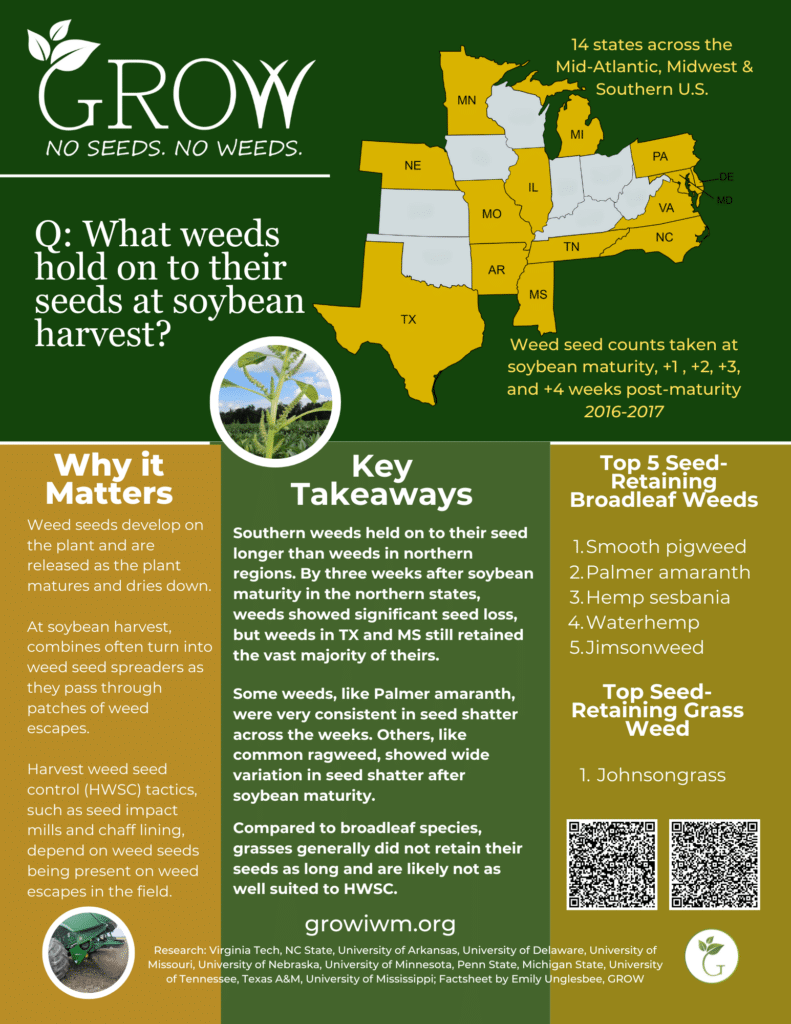
Learn When Weeds Shed Their Seeds (And Why It Matters!)
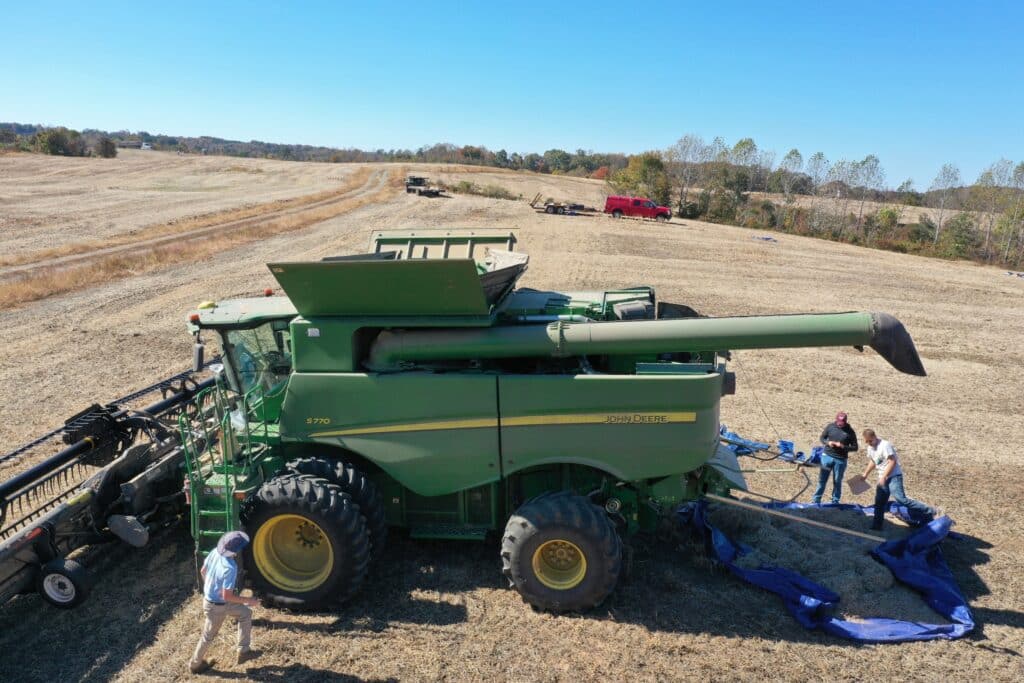
A Weed Seed Killing Machine: Testing the integrated Harrington Seed Destructor
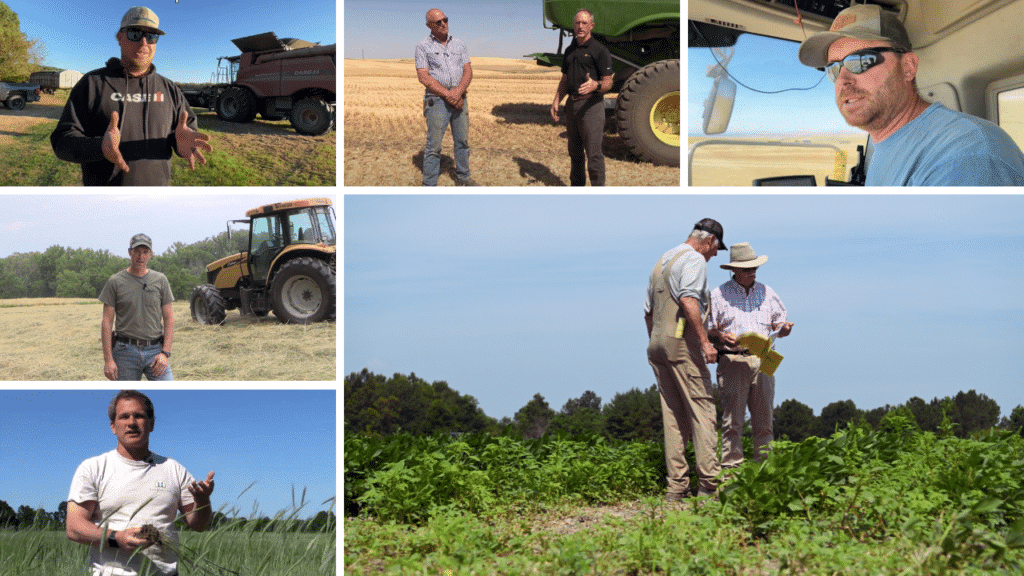
Learn from the Best: GROW Farmer Case Studies
Author
Ryan Hamberg, Texas A&M
Contributors
Luisa Baccin, Oregon State University
Muthukumar Bagavathiannan, Texas A&M
Marcelo Moretti, Oregon State University
Editors
William Curran, Penn State (emeritus)
Michael Flessner, Virginia Tech
Mark VanGessel, University of Delaware
Emily Unglesbee, GROW
Reviewer
Lynn Sosnoskie, Cornell University
Resources
Michigan State University, The Ohio State University. Basics of Electrical Weed Control https://www.canr.msu.edu/resources/basics-of-electrical-weed-control
Pokorny K, Moretti M, Oregon State University. Could weeds be controlled by zapping them? Extension is investigating. https://extension.oregonstate.edu/news/could-weeds-be-controlled-zapping-them-extension-investigating
Unglesbee E, After the Volts: Is Weed Electrocution Safe for the Soil? https://growiwm.org/after-the-volts-is-weed-electrocution-safe-for-the-soil/
Citations
Diprose, M. F., & Benson, F. A. (1984). Electrical Methods of Killing Plants. In J. agric. Engng Res (Vol. 30).
Diprose, M. F., Benson, F. A., & Hackam, R. (1980). Electrothermal control of weed beet and bolting sugar beet. Weed Research, 20(5), 311–322. https://doi.org/10.1111/j.1365-3180.1980.tb01625.x
Schreier, H., Bish, M., & Bradley, K. W. (2022). The impact of electrocution treatments on weed control and weed seed viability in soybean. Weed Technology, 36(4), 481–489. https://doi.org/10.1017/wet.2022.56
Slaven, M. J., Koch, M., & Borger, C. P. D. (2023). Exploring the potential of electric weed control: A review. Weed Science, 1–49. https://doi.org/10.1017/wsc.2023.38
Vigneault, C., & Benoit, D. L. (2001). Electrical Weed Control: Theory and Applications. In Physical Control Methods in Plant Protection. (pp. 174–188).